Systemlösung verspricht neue Effizienzpotenziale
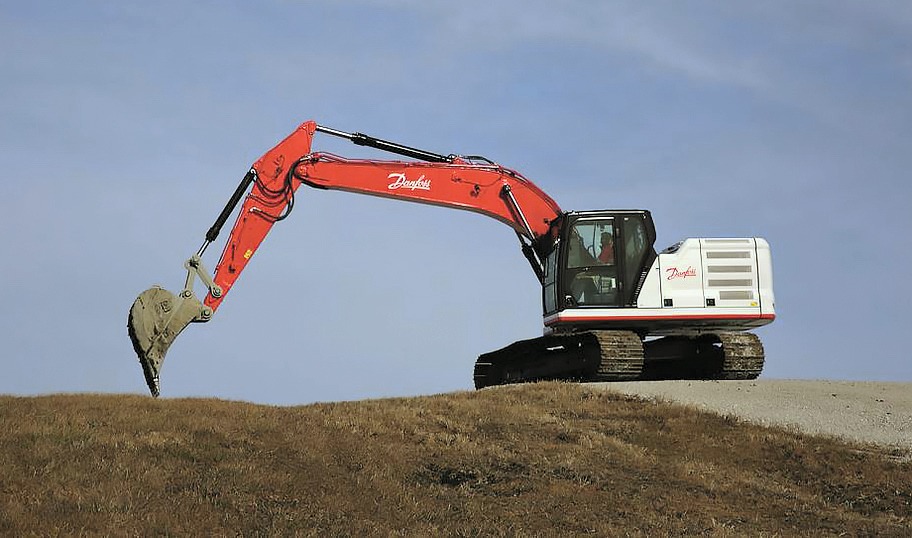
Mit der Dextreme-Systemlösung von Danfoss Power Solutions, Anbieter von Mobil- und Industriehydraulik sowie elektrischen Antriebssystemen, soll sich die Energieeffizienz von Baggern um 15 bis 50 Prozent verbessern, unabhängig vom Antriebsstrang. Die Lösung umfasst drei inkrementelle Systemkonfigurationen: Swap, Flex und Max.
Die einfachste Konfiguration Swap ersetzt die konventionelle Haupthydraulikpumpe des Baggers durch eine Digital-Displacement-Pumpe, kundenspezifische Software und ein digitales Steuergerät. Dadurch sinken laut Danfoss der Kraftstoffverbrauch und die CO2-Emissionen um 15 Prozent gegenüber einem Bagger mit herkömmlicher Hydrauliktechnologie. Die Konfigurationen Flex und Max bauen auf Swap auf, um noch höhere Einsparungen zu erzielen. Flex weist das Pumpenfördervolumen bedarfsgesteuert und dynamisch den jeweiligen Arbeitsfunktionen zu, wodurch Drosselverluste im Hauptregelventil reduziert werden können.
Dextreme Max ermöglicht Energierückgewinnung aus Baggerbewegungen wie etwa dem Abbremsen der Schwenkbewegung und dem Absenken des Auslegers sowie direkte Laststeuerung über die Pumpe selbst, wodurch Drosselungsverluste zusätzlich reduziert werden. Flex und Max sollen voraussichtlich Energieeinsparungen von 30 bzw. 50 Prozent ermöglichen. Herzstück ist die voll digital gesteuerte Hydraulikpumpe für Off-highway-Arbeitsmaschinen. Das digitale Steuergerät der Pumpe aktiviert jeden Kolben einzeln und ermöglicht so eine schnelle und genaue Reaktion auf Systemanforderungen, was eine bessere Steuerbarkeit der Maschine ermöglicht. Die Pumpe bietet hohe Voll- und Teillasteffizienz, da immer nur die Kolben verwendet werden, die zur Erfüllung des Bedarfs erforderlich sind.
Die Swap-Konfiguration mit schnellem Ansprechverhalten auf die Reglerimpulse der Digital-Displacement-Technologie ermöglicht eine erhebliche Verringerung der Motordrehzahl, ohne Gefahr zu laufen, dass der Motor abgewürgt wird. Das optimiert nicht nur den Kraftstoffverbrauch und die Emissionen, sondern auch den Geräuschpegel und verbessert so den Bedienkomfort.
Ist die Verkürzung der Zykluszeiten für den Maschinenbesitzer wichtiger als die Reduzierung des Kraftstoffverbrauchs, kann das System eine bis zu 25 Prozent höhere Produktivität erzielen, indem es die volle Drehzahlkapazität des Motors nutzt. Darüber hinaus vereinfacht die digitale Steuerung die Leistungsüberwachung und -diagnose.