Doka-Schalungskonstruktion für gewundenes Flugdach
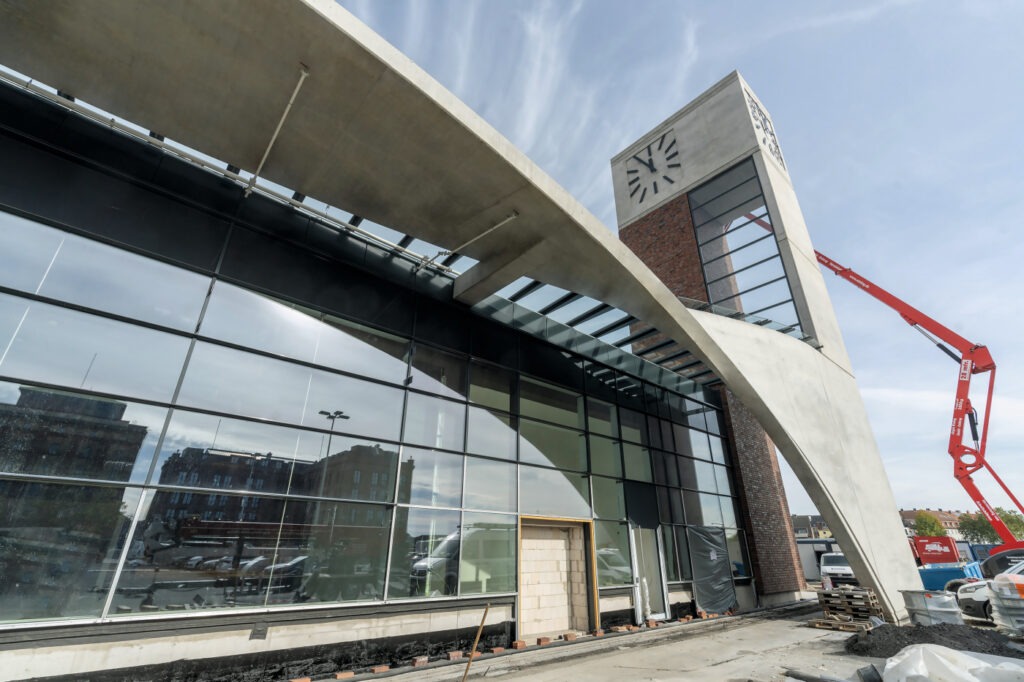
Der neue Hafenmarkt im Münsteraner Hansaviertel besticht mit viel Klinker und grazil wirkendem Sichtbeton. Im Osten wird das Areal durch einen 24 m hohen Uhrenturm begrenzt, dessen filigrane Beton-Südwand sich um 90 Grad verdreht und zum Vordach des angrenzenden Supermarkts wird. Schalungstechnisch eine große Herausforderung, die dank VR-Visualisierung von Doka doch anders gelöst wurde als ursprünglich geplant.
Im Stadthafen von Münster ist mit dem neuen Hafenmarkt ein nutzungsgemischter Standort aus Nahversorgern, Gastronomie, Dienstleistern, Praxen, Kitas, Wohnungen und einer Quartiersgarage entstanden. Das komplexeste Betonbauteil des Hafenmarkts ist der sogenannte Twist, ein Flugdach in 9 m Höhe, das um 90 Grad verwunden in die südliche Wand des Uhrenturms übergeht. Der 24 m hohe Turm markiert die östliche Begrenzung des Areals. Für die Schalungsplanung des Dachs erstellten die Doka-Techniker zur besseren Visualisierung ein 3D-Modell, das per VR begangen werden konnte.
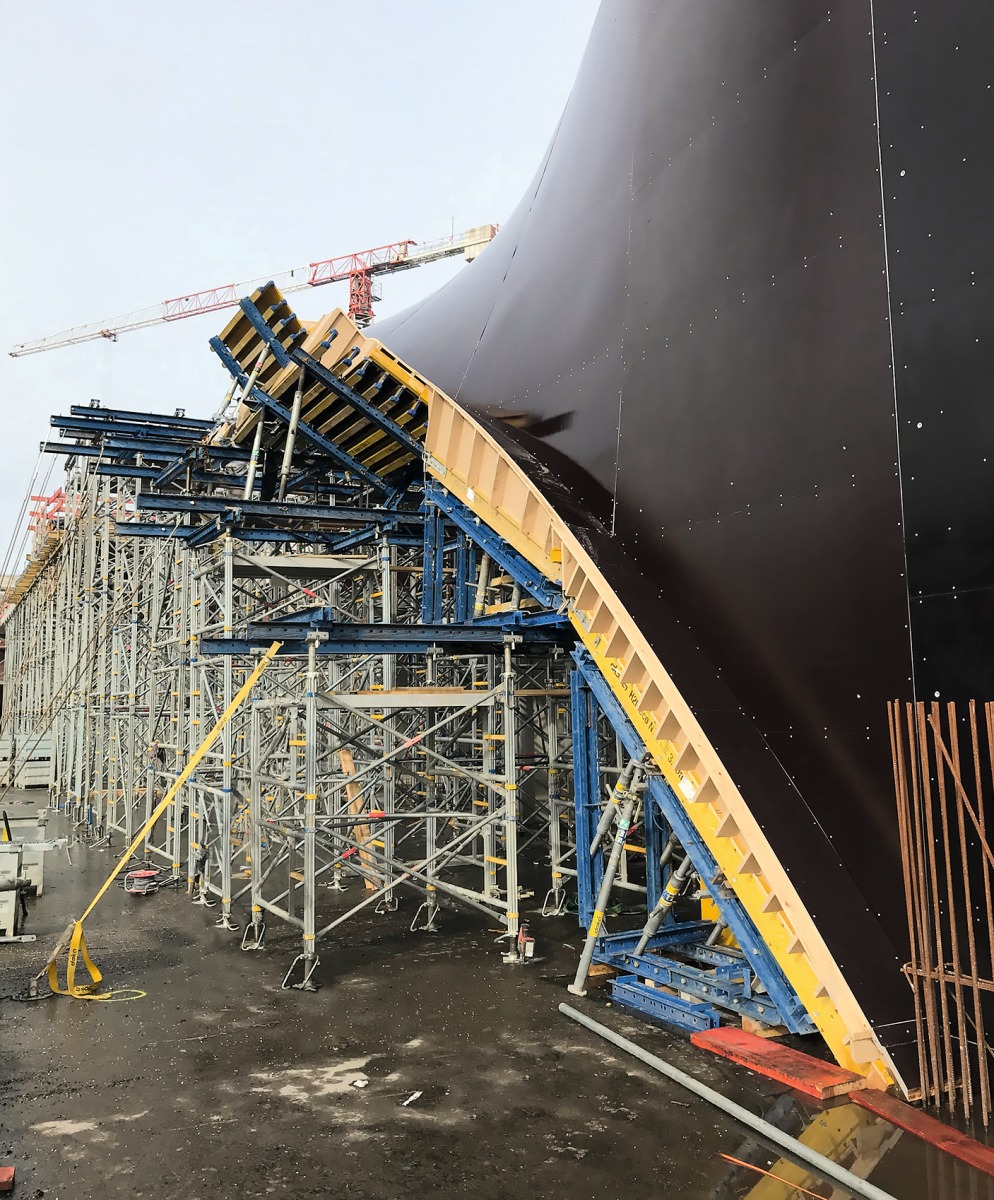
So erhielt die Baumannschaft des ausführenden Unternehmens Köster ein anschauliches Bild der tatsächlichen Bauteilgröße und -geometrie. Durch das 3D-Modell wurde der Bauleitung klar, wie filigran das Bauteil im freischwebenden Zustand wäre – und entschied sich dafür, zuerst den Supermarkt und dann den Twist zu bauen. Dieses Vorgehen entgegen dem ursprünglichen Plan erwies sich am Ende als zeit- und kostensparend, weil man sich etwa ein zweites Traggerüst zur Bauteilsicherung sparte und mit dem Bau des Supermarkts beginnen konnte, während parallel die Schalungsplanung für den Twist weiterging. In Summe erfolgte die Planung vollständig 3D-gestützt und wurde Köster neben den Schalungsplänen als AR-Modell zur Verfügung gestellt.
Und auch in der Umsetzung ließen sich Köster und Doka einiges einfallen, um den architektonischen und optischen Anforderungen (SB3) gerecht zu werden. So mussten ein Teil des insgesamt 40 m langen Flugdachs sowie die 90-Grad-Verdrehung zwar in Segmenten betoniert werden, es sollte aber nicht danach aussehen. „Das hieß kein Versatz zwischen den Übergängen. Bei diesen Gegebenheiten ist es eine Kunst, die Absätze so hinzubekommen, dass es hinterher wie aus einem Guss aussieht“, erklärt André Richter, Projektleiter bei Köster und mitverantwortlich für die tadellose Ausführung. „Außerdem gab es noch die Frage, wie das Regenwasser optimal abfließen sollte. Eine Edelstahlkante hätte optisch gestört. Also haben wir uns für eine im Beton eingelassene Regenrinne entschieden.“
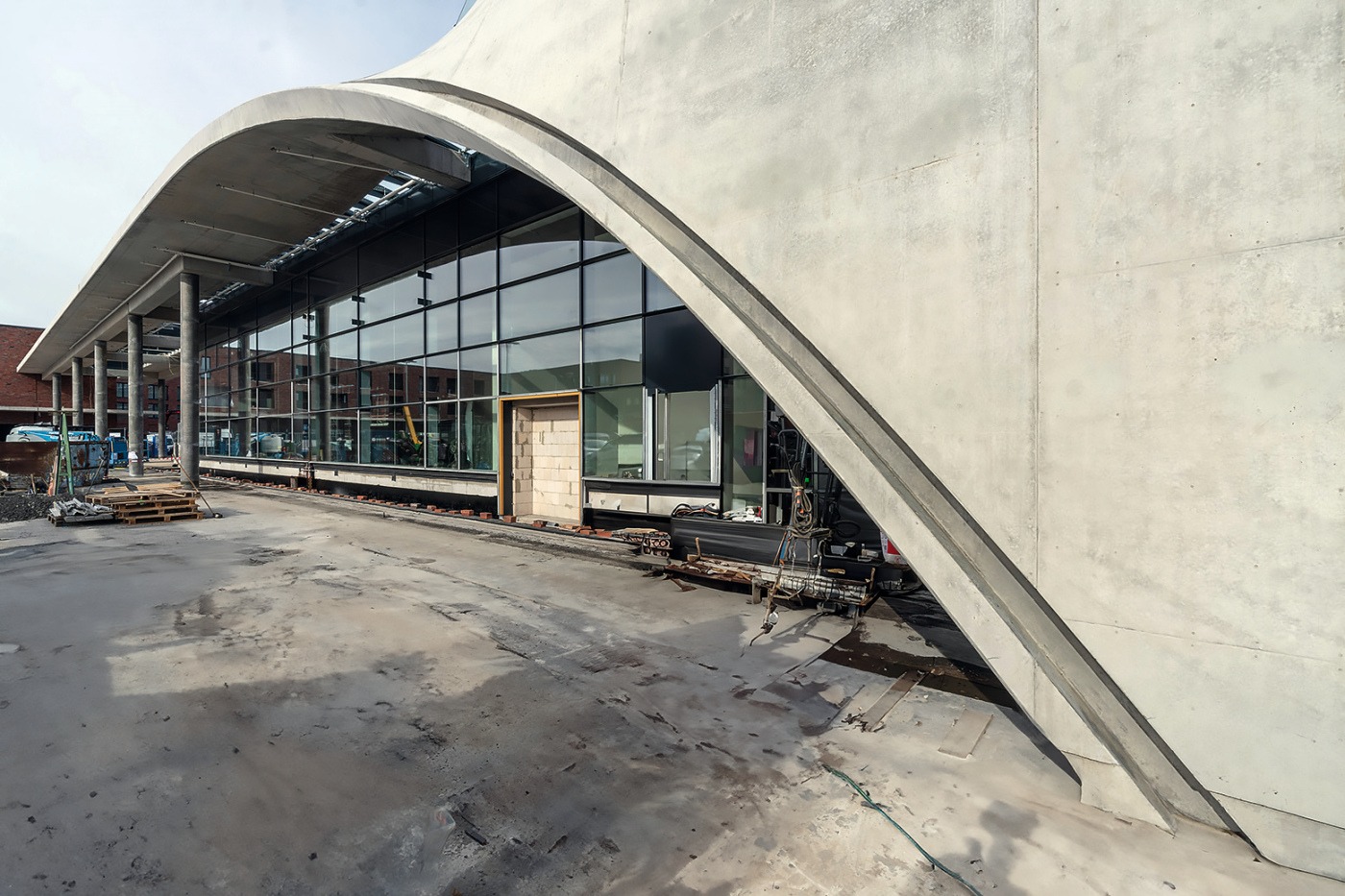
Als Schalungskonstruktion kamen sich neigende, speziell angefertigte Schalungselemente auf Spindelgespärre – mit Staxo-100-Türmen unterstellt – zum Einsatz. Die Planung der Schalungselemente wurde durch das Team der Doka-Montageplanung unterstützt. So konnten Flächenabwicklungen der Schalhaut erstellt werden, die den Schalhautzuschnitt der verwundenen Oberflächen inklusive der Ankerbohrungen per CNC ermöglichten. Das Ergebnis, insbesondere die dreidimensional gekrümmte Betonfläche, war für Baufirma und Bauherr mehr als zufriedenstellend.
Was beim Betonieren genau passiert
Xact-Load-&-Pressure-Sensoren von Doka überwachen den Betoniervorgang digital und in Echtzeit. Dessen ideale Steiggeschwindigkeit ist von vielen externen Faktoren abhängig, wie etwa der Witterung, der Betonmischung oder dem zulässigen Frischbetondruck der Schalung. Die Live-Daten der Xact-Sensoren helfen, mit bestmöglicher Geschwindigkeit zu betonieren – auch bei CO2-reduzierten Betonmischungen. Die Load-Sensoren lassen sich an gängigen Ankersystemen montieren und überwachen die Ankerlast. Der Pressure-Sensor wird dagegen an der Rückseite der Schalungsplatte montiert und zeigt den Frischbetondruck auf die Schalung an. Die kabellosen Sensoren sind wasser- und staubdicht und verbinden sich über Bluetooth mit Smartphones, auf denen die Xact-App den Frischbetondruck bzw. die Ankerlast in Echtzeit anzeigt. Die Xact-Sensoren sind bereits auf ersten Baustellen im Einsatz.