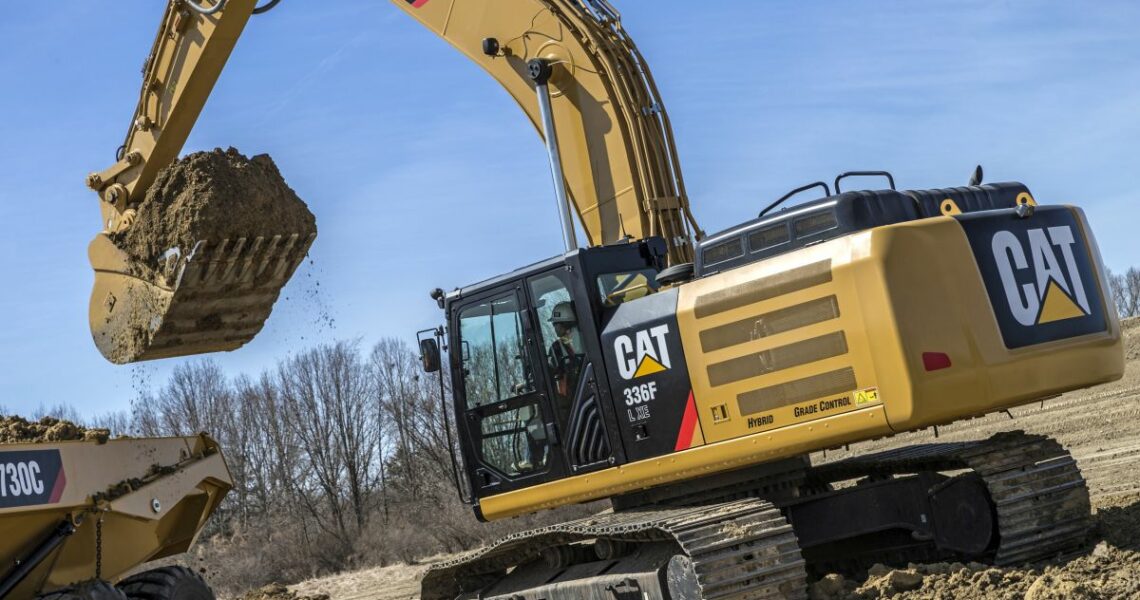
Diesel und Elektromotor in guter Symbiose
Ob umschaltbar, diesel-elektrisch oder rein elektrisch: Neue Antriebe für Baumaschinen stellen Hersteller und Betreiber vor große Aufgaben. Dazu gehört es auch, ungenutzte Energie aufzufangen, kurzzeitig zu speichern und bei Bedarf wieder in den Antrieb einzuspeisen. Doch nicht jeder Ansatz ist für jeden Maschinentyp geeignet. Und auch der Diesel hat noch lange nicht ausgedient.
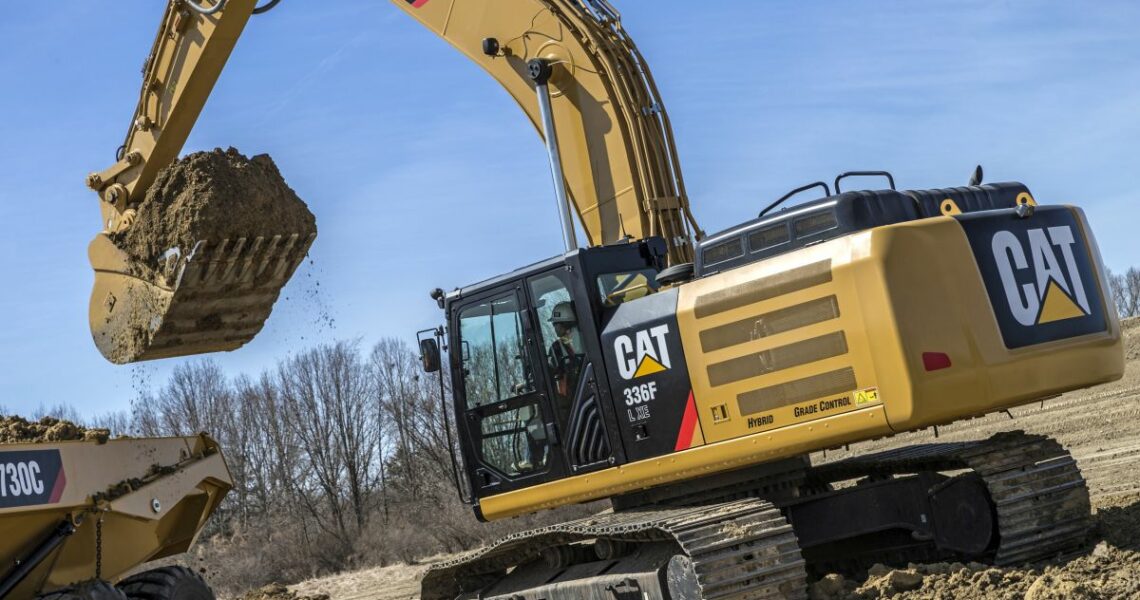
Am Bau wird hart gearbeitet. Baumaschinen, ob klein oder groß, dürfen deshalb keine Antriebsschwächen haben. Die zeichnen sich leider jedoch ab: Dieselmotoren, seit Jahrzehnten die treibende Kraft in fast allen Baumaschinen, sind ins Gerede gekommen, sollen sauberer arbeiten, weniger Rußpartikel und Feinstaub erzeugen. Der technische Aufwand für eine intensive Abgassäuberung aber ist mittlerweile enorm. Zugleich fordern immer mehr Ausschreibungen Baumaschinen sauberen Antrieben, oft wird bereits über Umweltzonen in Städten für Lkw und Baumaschinen debattiert. Kaum ist in Europa die Abgasstufe IV (entspricht Tier 4 in den USA) abgehandelt, zeichnet sich schon die EU-Stufe V mit ab 2019 noch weiter verschärften Grenzwerten ab. Und alle reden über CO2-Erzeugung, Feinstaub, Klimawandel und nachhaltige Energieerzeugung.
Eines steht unzweifelhaft fest: Energie ist viel zu kostbar, als dass sie auch bei Baumaschinen ungenutzt verpuffen darf. Zugleich benötigen die Maschinen für viele Arbeiten einfach auch viel Kraft und daher oft große Energiemengen. Energie aus fossilen Kraftstoffen wie Öl und Gas ist aber nur begrenzt vorhanden. Und regenerative Energie aus Wind, Sonnenlicht und Wasserkraft muss mit entsprechender Anlagentechnik erzeugt und verteilt werden. All dies verlangt Abbau und Aufbereitung diverser Rohstoffe, Herstellung und Transport, Bau und Wartung von Anlagen, dazu eine ausgedehnte Infrastruktur sowie unzählige Lkw und Maschinen – die dann wiederum ebenfalls viel Energie benötigen.
An der Rückgewinnung kostbarer, aber oftmals ungenutzter Energieanteile in Baumaschinen führt wohl kein Weg vorbei. Das jedoch erfordert komplexere Antriebssysteme, die Kombination mehrerer Antriebsarten sowie kompakte, leichte und robuste Energiespeicher. Insofern werden neue Antriebslösungen, die den spezifischen Arbeitsweisen der Maschinen, ihren typischen Bewegungen sowie den Voll- und Teillastphasen ihrer Motoren optimal angepasst sind, den standardisierten Diesel verdrängen. Anders als bei Pkw, Bussen und Lkw wird es für Baumaschinen jedoch keine Standardlösungen geben. Schon bei den Nutzungsprofilen und Lastverläufen gibt es keinen greifbaren Durchschnitt: Manche Motoren haben einen extrem hohen Volllastanteil, andere tuckern meist nur in Teillast. Einige Maschinen benötigen zum Fahren wenig Energie und für ihre Arbeit viel, andere bringen ihre gesamte Arbeitsleistung mit der Fahrbewegung auf.
Was im Einzelfall sinnvoll ist, muss von Maschine zu Maschine erwogen werden. Entsprechend breit ist das Ideenspektrum: Es umfasst etwa hydraulische und elektrische Energiespeicher, die nicht nur Energie zurückgewinnen, sondern auch – vom Motor bei weniger Kraftbedarf erzeugt – kontinuierlich auffangen und speichern. Dazu gehören auch innovative Radladergetriebe als Kombination von mechanischem und hydrostatischem Antrieb, umschaltbare Diesel- und Elektroantriebe, Gasantriebe oder auch diesel-elektrische Antriebe auf Wechselstrombasis.
Eine Erzeugung vor Ort macht noch immer Sinn
Im Vergleich zu elektrischen Antrieben, bei denen die Energie zur Maschine gebracht oder in ihr gespeichert werden muss, ist die Energieerzeugung direkt vor Ort in einem Verbrennungsmotor nach wie vor sinnvoll. Dessen größter Nachteil sind aber die unvermeidlichen Abgase, die besonders bei Dieselmotoren wegen der Feinstaubpartikel wachsender Kritik ausgesetzt sind. Deshalb wird nun häufig der Benziner als Alternative genannt – wegen der weniger schädlichen und einfacher zu reinigenden Abgase. Er hat aber bei gleicher Leistung einen höheren Verbrauch als der Diesel. Zudem erzeugt ein Benziner weniger Drehmoment beim Anfahren und bei niedrigen Drehzahlen. Gerade die aber sind vorteilhaft, weil kraftstoffsparend, lärmarm und motorschonend.
Benzin- wie Dieselmotoren verlieren den größten Teil ihrer Energie durch Wärme, weil die im Kraftstoff enthaltene Energie in Explosionshitze umgewandelt wird. Dabei erreichen Benziner nur einen Wirkungsgrad von knapp über 30 Prozent, ein einfacher Diesel dank Selbstzündung des Kraftstoffs bereits 39, mit Turbolader 41 und mit Ladeluftkühlung 44 Prozent. Zudem ist bei Benzinern mit mehr Volumen und Eigengewicht wegen größerer Tanks zu rechnen. Ähnliche Parameter gelten für Motoren mit Gasantrieb, die nun häufiger vor allem in Kompaktmaschinen zu finden sind. Antriebe mit Propan- und Flüssiggas (LPG), verdichtetem Erdgas (CNG) oder Flüssigerdgas (LNG) erzeugen zwar auch, aber deutlich sauberere Abgase.
Eine Frage der Reichweite
Nicht umsonst werden alle größeren Baumaschinen und Lkw von Dieselmotoren angetrieben. Der Verbrauch spricht hier einfach gegen den Benziner. Erinnert sei an den von 1952 bis 1959 gefertigten US-Panzer M48 Patton, der auch bei der Bundeswehr lief. Der 44-Tonner hatte einen 690 PS starken Benzinmotor und verbrauchte auf 100 km rund 670 Liter. Die Reichweite der ersten Serie betrug daher – auf ebener Straße, nicht im Gelände – gerade mal 70 Meilen, also rund 110 km.
Die Hürde bei Gasmotoren: Man braucht erheblich größere Tanks oder muss die Tankintervalle verkürzen. Deshalb greifen Anbieter gern auf handelsübliche Gasflaschen zurück, die am Einsatzort vorgehalten, leicht beschafft und im Handumdrehen ausgetauscht werden können. Solche Gastanks eignen sich jedoch nur für Kompaktmaschinen wie etwa die Radlader von Avant und Hesse, bei größeren Maschinen hätten die Gasbehälter bereits beträchtliche Dimensionen. Die weltweit ersten Gasstampfer von Bomag wiederum werden mit Propangas betrieben und belasten den Bediener praktisch nicht mehr mit Abgasen. Und die selbst wieder befüllbaren Gasflaschen ermöglichen lange Standzeiten.
Auch einige Motorenbauer widmen sich nun dem Gasmotor, so etwa Deutz mit dem TCD 2.2, der mit bis zu 55 kW Leistung vorwiegend für den Materialumschlag und kompakte Baumaschinen konzipiert wurde. Den Motor gibt es sowohl in Diesel- als auch Flüssiggasversion. Und auch der bewährte TCD 2.9 leistet nun als LPG-Gasvariante bis 55 kW und gleicht dabei in Größe und Ausführung seinem selbstzündenden Pendant. Scania ergänzte sein Portfolio jüngst um einen Gasmotor, der mit 16,4 l Hubraum vorrangig für Stromaggregate vorgesehen ist. Bei der Verwendung von Erdgas reduzieren sich die CO2–Emissionen nach Werksangaben um rund 20, bei Biogas um beachtliche 90 Prozent.
Diesel und Strom schließen neue Freundschaft
Scharf zu unterscheiden sind der umschaltbare Antrieb, bei dem zwischen Diesel- und Elektromotor gewählt werden kann, und der diesel-elektrische Antrieb, bei dem der Dieselmotor einen Generator antreibt, der dann für einen oder mehrere E-Motoren Strom erzeugt. Beide sind aktuell stark im Kommen.
Umschaltbare Antriebe sind attraktiv, wenn Maschinen häufig in Innenräumen oder sensiblem Umfeld arbeiten müssen – dort hat der leise, abgasfreie E-Antrieb enorme Vorteile. Damit kann sogar früher am Morgen, später am Abend oder nachts gearbeitet werden, ohne Beschwerden von Anwohnern fürchten zu müssen. Das gilt auch für längere Arbeitsphasen an einem konstanten Ort, wo die Maschinen ans Stromnetz angeschlossen werden können. Beispielhaft dafür etwa eine Hubarbeitsbühne von JLG oder der Prototyp eines Roto-Teleskopstaplers von Merlo mit angebauter Hubbühne oder Kranwinde: Im Elektrobetrieb ist der Diesel ausgeschaltet, zum Umsetzen und für andere Arbeiten bleibt er weiterhin voll nutzbar. Andere Beispiel sind raupenmobile Recyclinganlagen von Keestrack und Rubble Master.
Demgegenüber bieten diesel-elektrische Antriebe fabelhafte Möglichkeiten für die Rekuperation, also Rückgewinnung von Energie. Dazu wird der antreibende E-Motor einfach zum Generator umgepolt, der beim Abbremsen einer Schwenk- oder Senkbewegung Strom erzeugt. Der wiederum wird kurzzeitig in Superkondensatoren oder länger in Akkus gespeichert und kann jederzeit wieder in den Antrieb, nämlich den E-Motor eingespeist werden. Dieses Konzept wird gern als Hybridantrieb bezeichnet, obwohl ein Hybrid eigentlich nur das Zusammenlegen zweier verschiedener Antriebsarten kennzeichnet.
Fast die ganze Energie geht in die Arbeitsleistung
Ganz auf den Diesel verzichten rein elektrisch angetriebene Maschinen, meist kompakte wie der Bobcat-Minibagger E10, Kleindumper von Alitrack, Bergmann, DMS und Wacker Neuson oder Radlader von Avant, Kramer, Sherpa und Wacker Neuson. Der Wirkungsgrad der E-Motoren ist mit 94 bis über 97 Prozent sehr hoch. Anders als beim Diesel wird der weitaus größte Teil der hineingesteckten Energie weder in Abgase noch Wärme umgewandelt und ist auch nicht als Verlustleistung verloren. Sie kommt vielmehr der Arbeitsleistung zugute. Weitere Vorteile sind neben den Umweltaspekten die hohe Leistungsdichte in Relation zur Motorgröße und die gute Regelbarkeit. Außerdem verringern weniger Komponenten den Aufwand für Wartung und Service. So ist der bürstenlose E-Motor der Akkustampfer AS50e und AS30e von Wacker Neuson komplett wartungsfrei – das spart über die Hälfte der Betriebskosten.
Leider haben E-Antriebe aber auch mit Schwierigkeiten zu kämpfen: Die Energiedichte der Akkus ist noch nicht befriedigend, sodass nur wenige Stunden Betriebsdauer erzielt werden oder große und schwere Akkupakete nötig sind. Das erhöht nicht nur das Leergewicht einer Maschine, sondern verschlechtert Energiebilanz und Gesamtwirkungsgrad. Andererseits ist eine Stromzuführung per Kabel bei den allermeisten Mobilmaschinen nicht praktikabel. Also sind kabellose Elektro-Baumaschinen ausnahmslos kompakte Exemplare, vergeblich sucht man sie in größeren Gewichts- und Leistungsklassen, der Energiebedarf wäre einfach zu groß.
Eine Kabelversorgung wiederum wurde – abgesehen von semi-mobilen Umschlagmaschinen und Großbaggern, die über Stunden stationär arbeiten – bislang nur ein einziges Mal für eine große, hochmobile Baumaschine vorgesehen: Der US-Hersteller LeTourneau hat 1982 für seinen 13-m³-Radlader TCL-1000 einen rein elektrischen Antrieb mit Kabelstrom angeboten. Am Heck des Laders war ein mehrere Meter hohes, schwenkbares Auf- und Abrollsystem angebracht, damit sich das Kabel im Rangierbereich weit und sicher in der Höhe bis zu einem Mast spannen kann, den Boden nicht berührt und nicht beschädigt wird. Verkauft wurde kein einziges Exemplar.
Auch hinter dem Motor passiert so einiges
Gleichwohl eröffnen sich bei der Optimierung der Antriebstechnik durch unkonventionelles Denken interessante Lösungen – wie das hydraulische Start-Stopp-System von Atlas Weyhausen für den 5-t-Lader AR 65e. Es ist anders als eine konvetionelle Abschaltautomatik: Ist der Radlader weder im Fahr- noch Arbeitsmodus, schaltet sich der Motor ab – aber erst, wenn ein für den Neustart erforderlicher Druckspeicher befüllt ist. Durch jede Pedal- oder Lenkradbewegung startet der Motor neu und erreicht dank hydraulischem Energiespeicher in nur 0,2 Sekunden wieder die Nenndrehzahl, also wesentlich schneller als beim Beschleunigen von Leerlauf auf Vollgas oder beim Start mit dem Schlüssel. Die Batterie und der Anlasser kommen dabei nicht zum Einsatz, die volle Leistung ist sofort vorhanden. Das patentierte System wurde in über 150.000 Start-Stopp-Zyklen erprobt, reduziert die Betriebskosten und spart bis zu zwölf Prozent Kraftstoff pro Tag.
Auch für Hydraulik und Getriebe gibt es bereits vielversprechende Lösungen, so die von Caterpillar und Liebherr für Radlader mittlerer Größe entwickelten Leistungsverzweigungsgetriebe (CVT, Continuously Variable Transmission). Ursprünglich wurden solche Getriebe für Traktoren konstruiert, denn sie vereinen die Vorteile der Hydrostatik wie leichte und stufenlose Regelbarkeit mit dem hohen Wirkungsgrad eines mechanischen Antriebs mit Wandlerüberbrückung. Ein vergleichbares Getriebe namens HVT (Hydromechanical Variable Transmission) wurde im Joint-venture von Dana und Bosch Rexroth entwickelt. Durch die CVT-Technik entfällt der hydrodynamische Drehmomentwandler zwischen Dieselmotor und Getriebe. Das bringt je nach Einsatz 25 bis 30 Prozent weniger Dieselverbrauch, mehr Fahrkomfort, weil Drehmoment und Drehzahl kontinuierlich und nicht in Sprüngen wechseln, keine merklichen Schaltunterbrechungen durch permanente Kraftübertragung sowie annähernd konstante Motordrehzal im effizientesten Drehzahl- und Lastbereich.
Nach dem Motor müssen zudem weder hydraulische noch mechanische Kraftübertragungen folgen, es können auch Generator und E-Motoren sein. Also ein diesel-elektrischer Antrieb, wie er sich seit den 1950er-Jahren zigtausendfach in Lokomotiven, Hafenschleppern und Brecheranlagen sowie in großen Radladern und besonders in Muldenkippern bewährt hat. Bis auf Cat-Muldenkipper werden alle Modelle mit mehr als 150 t Nutzlast so angetrieben. Das Potenzial steckt in der Computer- und Regelungstechnik sowie der Rückgewinnung von Energie. Zudem lassen sich die Vorzüge elektrischer Antriebe nutzen, ohne auf Mobilität zu verzichten, denn das Kraftwerk wird ja in Gestalt von Dieselmotor und Generator in der Maschine mitgeführt. Das überzeugt immer mehr Hersteller und findet sich so beim Cat-Kettendozer D7E, bei neuen Hybrid-Radladern von Hitachi und John Deere wie auch beim Volvo-Laderprototyp LX01. Der besitzt zwar ebenfalls Dieselmotor, Generator und E-Motoren in den Radnaben, doch läuft der Diesel nur bei Bedarf. Er startet erst dann automatisch, wenn eine Batterie als Energiespeicher nur noch geringe Kapazität hat. Die Batterie speist die E-Motoren mit Strom, der Dieselmotor arbeitet nur beim Aufladen. Das Konzept soll den Dieselverbrauch um bis zur Hälfte verringern.
Braucht für gleiche Arbeit nur die halbe Leistung
Ein an der TH Köln entwickelter diesel-elektrischer Hybrid-Straßenfertiger (DEHS) bietet zwar keine Rekuperation, dazu sind die Bewegungen zu langsam, soll aber gegenüber herkömmlichen diesel-hydraulischen Modellen bis zu 60 Prozent weniger Kraftstoff verbrauchen. Der Fertiger kann stündlich die gleiche Menge Material bei gleicher Qualität einbauen wie die Serienmaschine, begnügt sich aber mit der halben Dieselmotorleistung. Statt durch ein Pumpenverteilergetriebe und acht Pumpenstränge arbeiten nun 16 drehende Antriebe elektrisch, die wichtigsten und leistungsstärksten mit hocheffizienten permanentmagneterregten Synchronmotoren.
Schon vor 22 Jahren stellte Vögele allerdings mit dem Super 1800 DE den weltweit ersten diesel-elektrischen Fertiger auf die Raupen, nur wurde der damals nicht als Hybrid-Straßenfertiger bezeichnet. Die Maschine war ihrer Zeit weit voraus und verbrauchte 40 bis 55 Prozent weniger Kraftstoff als mit konventionellem Antrieb. Die Wartungskosten reduzierten sich dank der fast wartungsfreien E-Antriebe sogar um 80 Prozent. Alle Aggregate wie Fahrwerk, Förderbänder, Verteilerschnecken und Einbaubohle wurden von Asynchron-Drehstrommotoren angetrieben, die durch Frequenzumrichter drehzahlverstellbar waren. Leider ging der innovative Fertiger mangels Kundeninteresse nicht in die Serienproduktion.
Jedes Quäntchen Energie wird optimal genutzt
Vielversprechender heute die Hybridmaschinen mit Rekuperation, bei denen Energie, die für bestimmte Bewegungen wie Schwenken oder Heben aufgewendet wurde, wieder zurückgewonnen und in den Antrieb eingespeist wird. Generell eignet sich die Rekuperation nur für größere Maschinen, bei denen sich durch Abbremsen schneller Bewegungen und schwerer Massen nennenswerte Energiemengen zurückgewinnen lassen. Der erste solche Bagger stammt von Komatsu, es folgten Cat, Hitachi und Kobelco. Liebherr modifizierte für den 350-t-Seilbagger HS 8300 HD das hydraulische Hybridsystem Pactronic, das schon längere Zeit für Hafenumschlagmaschinen genutzt wird. Zudem bietet Liebherr für einige Umschlagbagger bereits serienmäßig das patentierte ERC-System zur Energierückgewinnung, das auf einem mittig zwischen den Ausleger-Hubzylindern angeordneten Energiespeicherzylinder basiert. Darin wird gasförmiger Stickstoff beim Absenken des Auslegers komprimiert. Beim Anheben unterstützt die im Zylinder gespeicherte Energie die beiden Hubzylinder, sodass weniger Kraft erforderlich ist. Dies wiederum reduziert die Motorleistung und senkt daher den Dieselverbrauch.
Seltener sind Radlader mit Rekuperation, derzeit ist am deutschen Markt keiner erhältlich. Auf US-Märkten bietet John Deere 19-, 21- und 54-t-Radlader mit diesel-elektrischem Hybridantrieb an, Hitachi stellte einen 22-t-Prototyp vor. Doch nur LeTourneau (zum Mining-Konzern Joy gehörend, kürzlich von Komatsu übernommen) produziert bereits seit mehr als einem Jahrzehnt schwere Radlader (107 bis 267 t) mit Rekuperation. Die gewonnene Bremsenergie aus den vier elektrischen Radnabenmotoren kommt dem Hubsystem der Schaufel zugute. Ebenso selten sind Antriebe mit Rekuperation in anderen Baumaschinen. Zwar wurden in jüngerer Vergangenheit mehr als ein Dutzend Hybridmaschinen auf Messen präsentiert, doch schaffte es bis auf wenige Ausnahmen kaum eine in die Serienproduktion. Hamm stellte im vergangenen Jahr mit der HD+ 90i PH den Prototyp einer 9-t-Tandemwalze mit hydraulischer Rekuperation vor. In Phasen geringer Auslastung füllt eine vom Dieselmotor angetriebene Pumpe einen Druckspeicher, dessen Energie bei Lastspitzen wie beim Anfahren oder Aktivieren der Vibration oder Oszillation wieder der Hydraulik zukommt.
Auch Zulieferer beteiligen sich. So entwickelte Bucher Hydraulics aus Klettgau für Baumaschinen und besonders Bagger ein proportional vorgesteuertes Senkbremsventil mit patentiertem Rekuperationskonzept, das rund 20 Prozent Energie einspart und so ein Downsizing des Dieselmotors bei gleicher Arbeitsleistung erlaubt. Das Ventil sorgt für die Wiederverwendung einer Teilölmenge, die direkt in die Gegenseite des Zylinders eingespeist wird. Beim Senken des Auslegers wird der Pumpenförderstrom verringert, je nach System kann der eingesparte Förderstrom für andere Funktionen genutzt werden.
Mit Schwung in eine neue energetische Zukunft
Ein zunehmend interessanter Energiespeicher sind Schwungräder. Sie sind robust, verschleißarm und bieten eine große Energiedichte, besonders bei sehr hohen Drehzahlen ab etwa 30.000 bis über 50.000 U/min. Schwungräder können zudem gut von E-Motoren gespeist werden und Energie quasi portionsweise wieder an den Antrieb abgeben. Bislang wurden sie allerdings bei Baumaschinen so gut wie nie genutzt. Sandvik entwickelte vor einigen Jahren einen stationären Hybrid-Zweiwalzenbrecher, bei dem kurzzeitige Leistungsspitzen durch zwei Schwungräder an beiden Seiten der Brecherwellen kompensiert wurden. Die Schwungräder speicherten mit ihrer Eigenmasse viel kinetische Energie, die bei schwer drehenden Brecherwellen sofort abgegeben wurde und damit den Antrieb unterstützte.
Vor vier Jahren stellte Ricardo einen Mobilbagger vor, bei dem ein Schwungrad zu Kraftstoffeinsparungen von mehr als 10 Prozent führte. Mit einem am Heck des Oberwagens angeordneten Hochgeschwindigkeits-Schwungrad wurde Energie von Ausleger und Schwenkwerk zurück gewonnen und für das Heben des Auslegers wiederverwendet. Unlängst präsentierte Joy den 7,2-m³-Untertagelader 22HD mit Kinetic-Energy-Storage-System (KESS): Die Nutzung der Bremsenergie in einem Schwungrad soll den Dieselverbrauch um 30 Prozent reduzieren. Das System unterstützt den Antrieb zeitweise mit über 50 Prozent, was den Lader schneller beschleunigen lässt und die Taktzeiten erheblich verkürzt. Die Schwungradtechnik soll die doppelte Energiemenge speichern als die Superkondensatoren, die bei manchen Hybridmaschinen bisher als Kurzzeit-Energiespeicher dienen.
Ob Schwungrad, elektrische oder hydraulische Energiespeicher, es scheint weiterhin sicher, dass der Dieselmotor zumindest größeren Baumaschinen ab etwa 10 t Gewicht auf lange Sicht erhalten bleibt. Derzeit existiert keine andere Kraftquelle, die der Mobilität und den Einsatzprofilen der meisten Baumaschinen so ideal entspricht. Deshalb werden die Maßnahmen zur Abgasreinigung mit großer Wahrscheinlichkeit nicht bei EU-Stufe V enden, sondern die Konstrukteure auch künftig beträchtlich fordern.