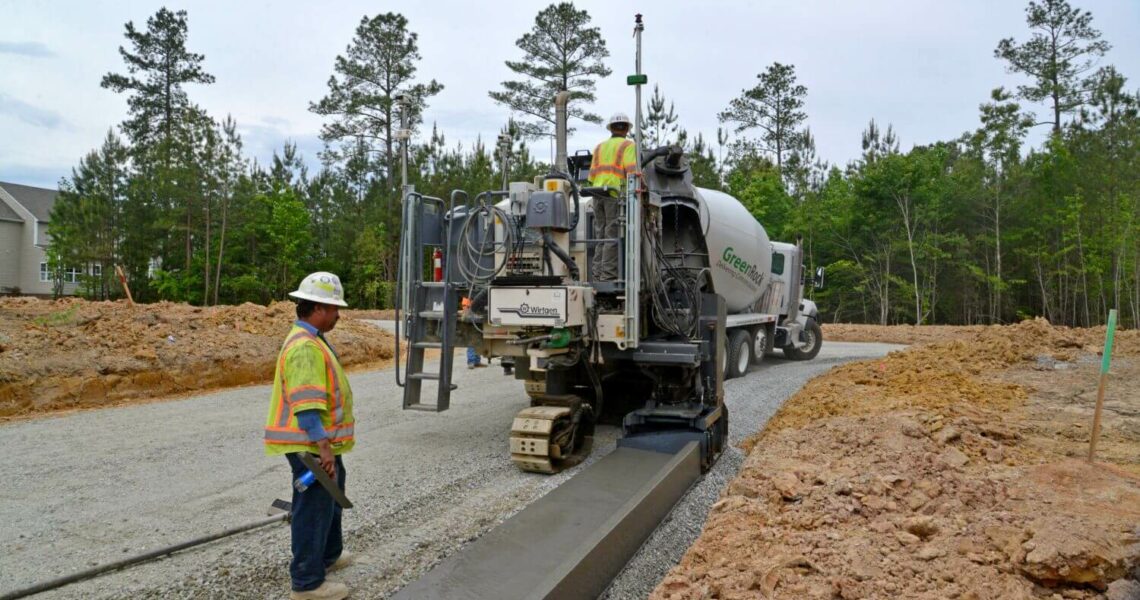
Autopilot 2.0: Zeitersparnis beim Betoneinbau
Betondienstleister Clay Armstrong arbeitet seit Kurzem mit dem neuen Autopilot 2.0 von Wirtgen. Ausgelegt für die Gleitschalungsfertiger SP 15i und SP 25i, ermöglicht das einfach zu bedienende 3D-System den leitdrahtlosen Betoneinbau im Straßenbau. Dem Firmenchef zufolge spielt es vor allem bei Verbundradien oder Tangentenabschnitten, die schnurgerade sein müssen, seine Stärken aus.
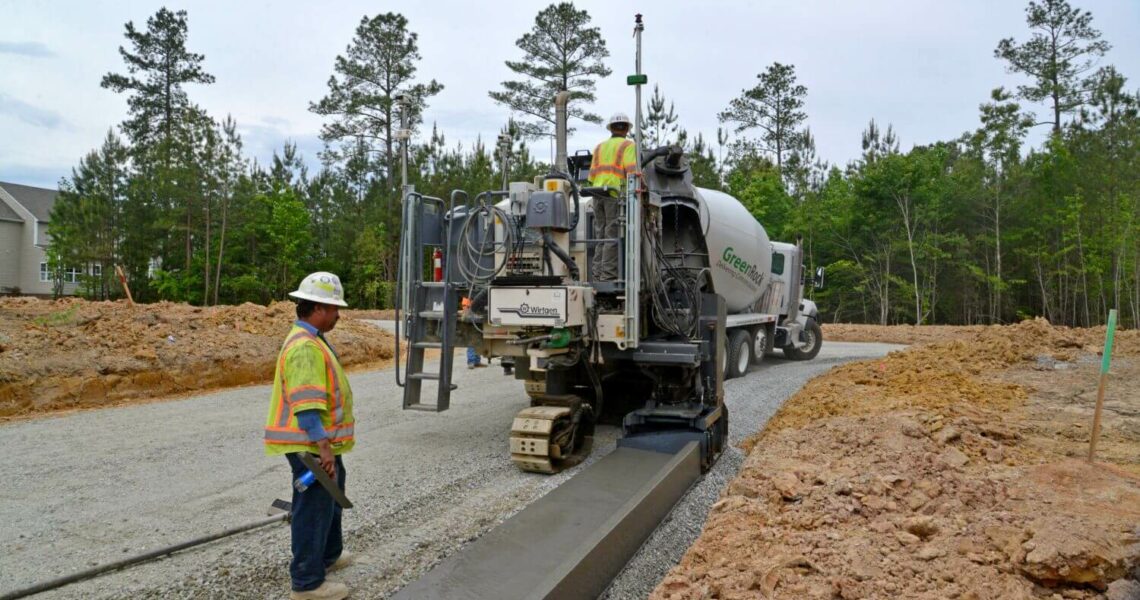
Die Firma Talley & Armstrong, ein Betondienstleister aus Virginia, gehört zu den ersten Unternehmen in Nordamerika, die beim leitdrahtlosen Betoneinbau auf den neuen Autopilot 2.0 von Wirtgen setzen. Ausgelegt für die Wirtgen-Gleitschalungsfertigern SP 15i und SP 25i soll er das Vermessen, Aufspannen und Demontieren von Leitdrähten überflüssig machen. Das 3D-System eignet sich beispielsweise für den Einbau von Betonschutzwänden, Bordsteinen, Rinnenprofilen oder Verkehrsinseln, aber auch für Fahrbahnen mit einer Breite bis 3,5 m im Inset- und 2,5 m im Offsetverfahren. Es umfasst ein Tablet, das sowohl die Maschinensteuerung übernimmt als auch am Field-Rover-Lotstab befestigt wird. Zwei auf der Maschine montierte GPS-Empfänger kommunizieren mit einer GPS-Referenzstation auf der Baustelle. Das satellitengestützte Navigationssystem (GNSS) steuert Lenkung und Querneigung des Gleitschalungsfertigers vollautomatisch. In Kombination mit einem Ultraschallsensor oder einer robotergesteuerten Totalstation steuert es außerdem präzise die Maschinenhöhe.
Dank einer zertifizierten Standardschnittstelle sind der SP 15i und SP 25i auch mit 3D-Systemen anderer Anbieter kompatibel. Die Daten werden mittels 3D-Schnittstelle an die Maschine übertragen. Beim Einbau kommen verschiedene Systeme wie etwa der GNSS-basierte RTK-Empfänger oder automatische Totalstationen zum Einsatz. Während des Einbauvorgangs ermöglichen die Sensoren auf der Maschine präzise Messungen. Die Systeme gleichen Soll- und Istwerte der Einbauparameter ständig ab. Wenn für ein Projekt kein digitales, dreidimensionales Geländemodell zur Verfügung steht, kann mit dem Field Rover von Wirtgen ein neues Datenmodell direkt auf der Baustelle erzeugt werden.
„Der leitdrahtlose Einbau mit dem Autopilot 2.0 hat für uns viele Vorteile“, erklärt Firmenchef Clay Armstrong. „Da ist zunächst der entfallende Zeitaufwand für das Setzen der Leitdrähte. Ein weiterer Faktor sind die gesparten Kosten für die Beschaffung des Drahts und der Drahthalter.“ Schmunzelnd erinnert er sich an den ersten Einsatz des Systems: „Wir hatten den Auftrag, ein Bordstein- und Rinnenprofil auf einem Parkplatz einzubauen. Am Ende des ersten Arbeitstags hätten meine Mitarbeiter normalerweise den Leitdraht abgebaut und auf dem nächsten Abschnitt neu gespannt. Stattdessen fragten sie, was sie tun sollten. Es gab keine Leitdrähte, die entfernt oder neu gesetzt werden mussten. Das war eine direkte Kostenersparnis.“ Armstrong zufolge spielt der Autopilot vor allem bei Verbundradien oder Tangentenabschnitten, bei denen es darauf ankommt, dass alle Tangenten schnurgerade sind, seine Stärken aus.
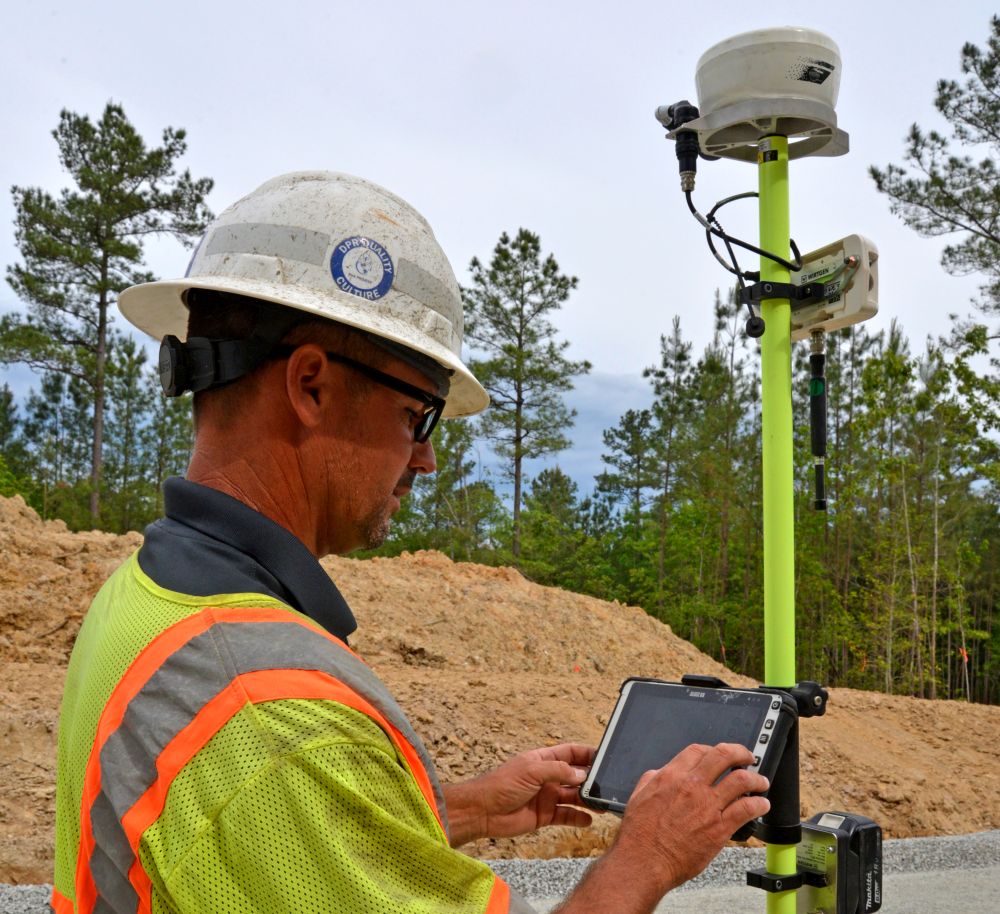
Der Autopilot 2.0 soll dabei noch leichter zu bedienen sein als die Vorgängerversion. „Das Tablet, das wir sowohl auf dem Fahrstand als auch mit dem Field-Rover-Lotstab verwenden, hat ein wesentlich besseres Display. Wir können jederzeit Änderungen am Modell vornehmen – unabhängig davon, ob es importiert oder aus Bodenpunkten oder den üblichen Absteckpunkten für Bordstein- und Rinnenprofile erstellt wurde“, so Armstrong weiter. Muss ein Modell korrigiert werden, lässt sich sowohl die vertikale als auch die horizontale Ausrichtung während des Einbauprozesses anpassen.
Änderungen im vertikalen Kurvenverlauf waren mit der Vorgängerversion schwierig oder teilweise gar nicht möglich. Armstrong: „Wir können einzelne Punkte zu einer vertikalen Kurve ändern und sie so weit auseinanderziehen, wie es erforderlich ist, um einen Verlauf zu glätten. Wenn wir beispielsweise wissen, dass Punkt A und Punkt B durch eine gerade verlaufende Gradiente miteinander verbunden sind, können wir theoretisch alle Zwischenpunkte löschen, die damit nicht übereinstimmen – oder zum ursprünglichen Modell zurückkehren. Wir können auch den prozentualen Verlauf der Gradiente im Modell ändern, wenn wir feststellen, dass sie mit den Bedingungen vor Ort nicht vereinbar ist.“ Mit dem tragbaren Field Rover lassen sich die Einläufe während des Einbaus überprüfen, mithilfe von Kontrollpunkten passt Armstrong das importierte Modell an die jeweilige Aufgabe an. Der kleinste Radius, den er bisher mit dem Autopilot 2.0 eingebaut hat, betrug 60 cm.
Zum reibungslosen Betoneinbau tragen auch die durdachten Features des Gleitschalungsfertigers SP 15i bei, wie etwa sein funktionaler, ergonomisch gestalteter Fahrstand. „Die Sichtverhältnisse sind gut“, sagt Armstrong. „Man hat die Förderschnecke des Trichters ebenso im Blick wie den Beton, der in die Schalung gefördert wird. Und das Betonprofil, das die Schalung verlässt.“ Der Firmenchef zieht die Förderschnecke dem Förderband vor, weil sie größere Betonmengen bevorraten kann. Dies ist besonders beim Einbau von Radien wichtig, wo sich eine Unterbrechung negativ auf die Einbauqualität auswirkt. Bei Talley & Armstrong sind acht Wirtgen-Schalungen im Einsatz: vom 15 cm breiten Bordsteinprofil bis zur 1,5 m breiten Gehwegschalung. Eine Adapterplatte bietet außerdem die Möglichkeit, Schalungen anderer Anbieter an den SP 15i anzubauen.
Clay Armstrong
Firmenchef, Talley & Armstrong, Henrico (Virginia)
„Wenn wir nicht mit einem importierten Modell arbeiten, kann es passieren, dass wir in einer Stichstraße zwei Stunden brauchen, um die erforderlichen Leitdrähte zu setzen. Beim Autopilot-System kann ich stattdessen mit dem Field Rover die entsprechenden Datenpunkte eingeben und innerhalb von nur zehn Minuten einen virtuellen Leitdraht erstellen.“