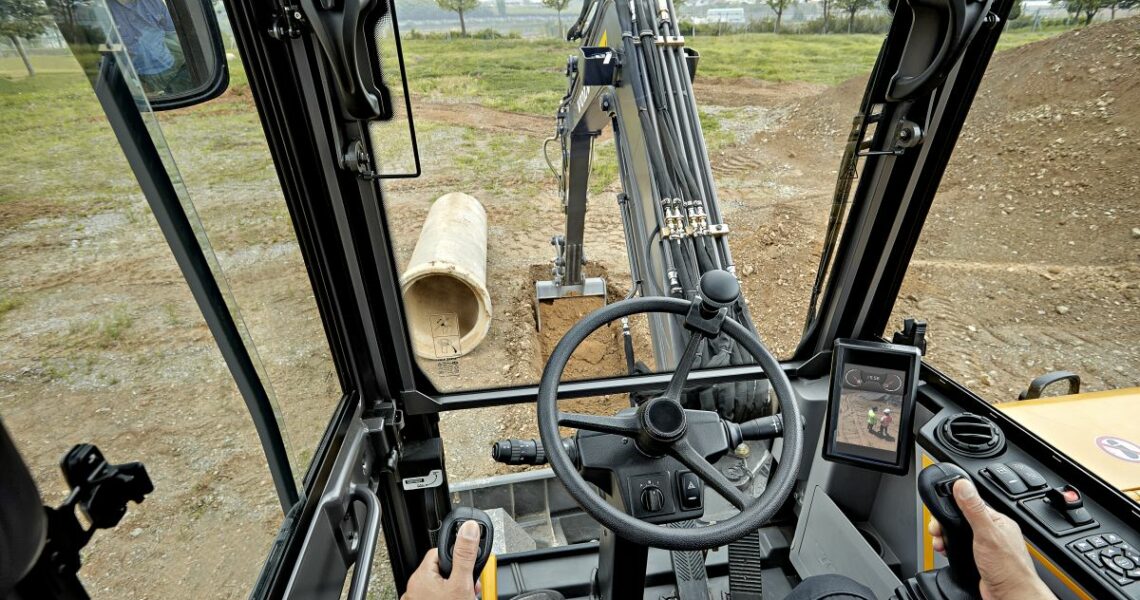
Der Mensch ist alternativlos
Die Bedienung moderner Baumaschinen stellt teils widersprüchliche Anforderungen, da vom Fahrer immer mehr Informationen schnell und sicher aufgenommen und verarbeitet werden müssen. Zudem gibt es wegen der großen Vielfalt und Unterschiedlichkeit der Aufgaben auch keine einheitliche Schnittstelle zwischen Mensch und Maschine.
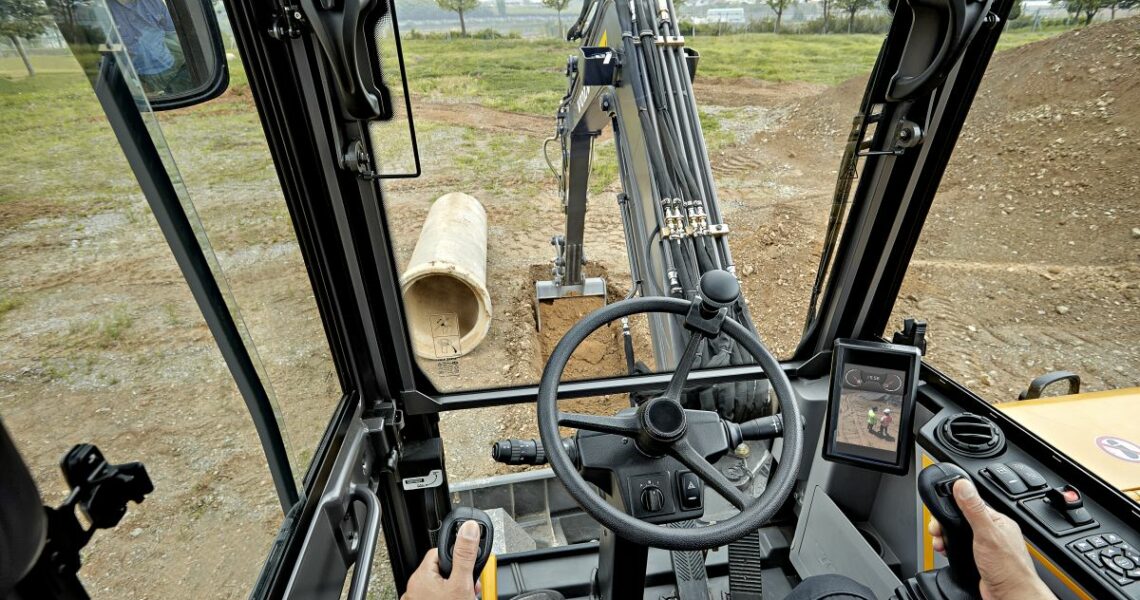
- Informations- und Steuerungssysteme müssen beherrschbar bleiben
- Unterschiedliche Baumaschinen brauchen unterschiedliche Bedienkonzepte
- Viele Anforderungen an die Kabine sind widersprüchlich
- Informationsflut überfordert auch geübte Bediener
Vollautomatische Baumaschinen wird es auf lange Sicht nicht geben. Ob Bagger, Radlader oder Dozer, Fertiger, Walze oder Straßenfräse, ob Teleskopstapler oder Turmdrehkran: Auch zukünftig wird ein Mensch als Bediener unverzichtbar bleiben. Nur er kann mit seinen Sinnen Situation und Umfeld auf einen Blick erfassen, kann entscheiden und kontrollieren, kann in Bruchteilen von Sekunden neue, besser angepasste Entscheidungen treffen und die Bedienung der Maschine dementsprechend ändern. Bei automatischen Baumaschinen wäre dazu eine immense Zahl von Sensoren nötig. Ebenso eine sehr aufwendige Simulation zum Erschaffen einer Software, die sämtliche Einflussparameter wie Boden, Gelände, Anbaugeräte, Baustelle, Personal, Wetter, andere Maschinen sowie wechselnde Aufgabenstellungen berücksichtigen können müsste.
Bauarbeiten, Baustellen und Baumaschinen sind zu vielfältig, zu variantenreich, als dass der Mensch durch Sensorik und Automation in naher Zukunft gänzlich ersetzt werden könnte. Zwar gibt es zunehmend mehr Teilautomatisierungen und Assistenzsysteme, doch handelt es sich dabei – verglichen mit dem gesamten Einsatz- und Anwendungsspektrum einer Baumaschine – nur um kleine Teilbereiche. Umso mehr Bedeutung kommt dem Fahrer zu. Er muss tagein, tagaus, in jeder Sekunde mit seiner Maschine interagieren. Er muss schnell und korrekt sich schlagartig ändernde Situationen erkennen und beurteilen, muss sicher zwischen Blicken auf Anbauwerkzeug, Umfeld, Display, Monitor, Bedienelemente und Anzeigewerte wechseln können, muss unzählige Informationen so schnell wie möglich erfassen und danach seine Entscheidungen treffen. Ganz wichtig dabei: die Schnittstelle zwischen Mensch und Maschine, das Human-Machine-Interface (HMI). Sie entwickelt sich heute auch bei Baumaschinen zu einem immer bedeutenderen Forschungs- und Industriezweig.
Kaum etwas beeinflusst die Effektivität und Qualität der Arbeit mit einer Maschine so stark wie das Fahrerhaus. Direkt davon abhängig sind Arbeitstempo, Produktivität und Betriebssicherheit. Fahrerhaus und Kabineninneres samt HMI sind die Kernelemente eines jeden Maschineneinsatzes.
Ein gutes Beispiel dafür ist der Kabinenentwurf Genius Cab, der an der TU Dresden gemeinschaftlich vom Concept Cab Cluster (CCC) entwickelt wurde. Dazu gehören OEM-Zulieferer wie Aurora, Fritzmeier, Grammer, Hella, Hydac, Mekra Lang, Savvy und Lumod sowie das Bauunternehmen Max Bögl, Wissenschaftler der TU und der VDBUM. Das Konzeptfahrerhaus soll durch Human Centered Design überzeugen. Ziel ist auch, den Maschinenherstellern das große Potenzial effizienter Systemintegration zu verdeutlichen. Entsprechend wurde in die Genius Cab zukunftsweisende Technik der Clusterpartner integriert. „Das Leitmotiv Human Centered Design setzt durch den hochwertigen, großzügig dimensionierten Innenraum den Fokus auf einen maximal ergonomischen Arbeitsplatz. Durch konsequente Systemintegration und kompromisslose Ausrichtung auf den Bediener wird die Arbeitssicherheit erhöht und die Effizienz gesteigert“, so eine Information der TU Dresden. Wanja S. Steinmaier, Geschäftsführer der Agentur Lumod, die mit der TU Dresden für das Design der Kabine verantwortlich ist, ergänzt: „Die Stichworte lauten Informationsmanagement und Klarheit. Entsprechend gibt es nur noch einen zentralen Touch-Monitor. Die emotionale Ansprache des Nutzers folgt dem gestalterische Ansatz zum Trend des Cocooning und trägt so dem Schutz- und Wohlfühlbedürfnis des Menschen Rechnung.“
Allen Bemühungen, neue Kabinen- und Bedienkonzepte zu entwickeln, steht entgegen, dass neue gesetzliche Abgasvorschriften und daraus resultierende bauliche Veränderungen an vielen Baumaschinen einen gegenteiligen Effekt bewirken. Denn die Komponenten zur Abgasnachbehandlung beanspruchen viel Bauraum und schränken daher den Platz und die Fahrersicht ein. Umfangreiche Systeme zur Abgassäuberung sind nicht in einem Stecknadelkopf unterzubringen. Nach der Abgasstufe IV wird für 2019 die Stufe V mit weiter verschärften Werten erwartet. Doch Baumaschinen lassen sich auf EU-Weisung nicht mit beliebig viel Peripherietechnik um den Motor herum vollstopfen. Einiges Kopfzerbrechen bereiten den Ingenieuren daher die unvermeidlichen Einschränkungen der Sichtverhältnisse für den Fahrer – trotz noch so moderner Kabinen.
Bei Baumaschinen ist alles ganz anders
Sämtliche Baumaschinen fallen zudem durch eine Besonderheit auf: Es gibt keine auch nur im Ansatz einheitliche HMI. Bei einem Bagger, dessen Fahrer sich ständig auf das Hin- und Herschwenken und zielgenaue Abstoppen des Oberwagens konzentrieren muss, gestaltet sich diese Schnittstelle gänzlich anders als bei einer Kaltfräse, deren Fahrer oft im Stehen arbeitet und von einer Maschinenseite zur anderen wechselt, um exakt Randbereiche und Bordsteinkanten beobachten zu können.
Ebenso unterscheidet sich die HMI eines Radladers, dessen Fahrer gut die Hälfte seines Arbeitstags im Rückwärtsgang verbringt, völlig von der eines knickgelenkten Muldenkippers, der sich einerseits auf unübersichtlichem Baustellenterrain so schnell wie möglich bewegen soll, andererseits aber nach jeder Fahrt zügig und sicher rückwärts unter den Bagger oder zum Abkippen rangiert. Man kann auch nicht die HMI eines Graders mit seiner äußerst komplexen Bedienweise und Multifunktions-Joysticks mit der eines Großdrehbohrgeräts, das sich nur selten bewegt und fast stationär an einer Stelle arbeitet, in einen Topf werfen. Diese erheblichen Unterschiede verhindern, dass bei Baumaschinen – abgesehen von weltweit verkaufter „Massenware“ wie Kompaktmaschinen – die Kabinen und Bedienelemente in Großserien zu standardisieren sind. Werden Maschinen zudem mit neuen Assistenzsystemen und 2D- oder 3D-Steuerungen ausgestattet, liegen häufig nicht einmal Erfahrungen vor, wie die HMI entsprechend umzugestalten und zu optimieren wäre.
Darüber hinaus sind die Größe und das Umfeld der Maschinen für die HMI enorm wichtig: So ist es durchaus ein Unterschied, ob der Fahrer einen 100-t-Laderkoloss mit über 800 PS Motorleistung in einem Steinbruch bewegt oder einen 2-t-Lader in den engen Baustellengrenzen einer Fußgängerzone. Oder ob er das Werkzeug eines 70-t-Abbruchbaggers in 20 m Höhe am Long-Front-Ausleger dirigiert oder mit einem Radlader und angebautem Gabelträger Paletten von einem Lkw entlädt.
Oft braucht es individuelle Sonderlösungen
Die Vielfalt bei Baumaschinen ist schier grenzenlos, und das ist ein nicht zu unterschätzendes Problem: Mag der Arbeitsplatz des Fahrers ideal sein, um alltägliche Aufgaben bestens durchführen zu können, wandelt er sich unversehens zur Problemstelle, sofern über Tage oder gar Wochen mit einem Anbaugerät gänzlich andere Arbeiten anfallen – und damit auch veränderte Anforderungen an den Fahrer. Insofern ist die Thematik bei Baumaschinen oft deutlich komplexer als bei anderen Fahrzeugen und Industriemaschinen. Und eine große Herausforderung für die Hersteller – von Baumaschinen selbst wie von Kabinen, Fahrersitzen, Displays, Joysticks und anderen Komponenten. Deshalb scheuen sich viele Baumaschinenhersteller, Fahrerhäuser einfach mit Industriekomponenten aus der Großserienproduktion zu bestücken, die am Markt zu günstigen Kosten verfügbar sind, sondern setzen lieber auf maßgeschneiderte Sonderanfertigungen wie spezielle Fahrersitze oder Joysticks.
Beim Entwurf eines Fahrerhauses und beim Optimierern der HMI sehen sich die Konstrukteure daher mit einer Vielzahl sich teils sogar widersprechender Parameter konfrontiert. Das betrifft die Größe der Fensterflächen und die Stabilität des Kabinenrahmens, die einfache Reinigung von Innenraum, Scheiben und Rückspiegel, das Volumen von Ablage- und Stauraum, genügend Freiraum für zusätzliche Kontrollboxen, Displays, Wägesysteme und Maschinensteuerungen, die Erreichbarkeit von Schaltern und Tasten oder auch das blendfreie, fehlerlose Erkennen wichtiger Anzeigeinformationen. Oder ob der Fahrer seinen Sitz oft, sehr oft oder nur selten verlassen und aussteigen muss. Ob er beim Auf- und Absteigen und nur einer Tür eventuell täglich etliche Male um die Maschine herumgehen muss. Wie oft er sich im Alltag mit Kollegen verständigen muss – dann sollten sich Türen arretieren und Fenster weit öffnen oder aufschieben lassen. Wenn der Fahrer häufig nach hinten oder zur Seite blicken muss, was dann seine Sicht behindern oder ihn veranlassen könnte, übervorsichtig und deshalb langsamer zu arbeiten.
Zur reibungslosen Interaktion des Fahrers mit seiner Maschine gehört heute auch der komfortable, einfache Umgang mit unterschiedlichen Anbauausrüstungen. Hilfreich ist hier das Abspeichern der Hydraulikdaten von hydraulisch betriebenen Anbaugeräten. Einige Bagger bieten dies für etwa fünf bis zehn Anbaugeräte. Zum Beispiel erfolgt die schnelle Einstellung der Zusatzsteuerkreise bei den neuen 6- bis 10-t-Baggern von Wacker Neuson über einen Jog Dial – ein aus dem Automobilsektor bekanntes System. Die individuellen Einstellungen der Anbaugeräte lassen sich damit auch während des Arbeitens durchführen. Und weil die Hydraulikdaten nach jedem Ausrüstungswechsel wieder abrufbar sind oder, wie bei manchen Systemen, automatisch erkannt werden, erspart sich der Fahrer viel manuelles Einstellen und damit kostbare Bedienungszeit.
Die unterschätzten Zwerge sind Protagonisten der Sicherheit
Klein, aber fein sollen sie sein, die Displays in neuen Maschinen aller Art. Klein, damit sie die Fahrersicht nicht beeinträchtigen, und fein, damit sie sämtlichen Anforderungen genügen. So sollen sie nicht nur Daten und Informationen über Ist-Zustände anzeigen, sondern beispielsweise bei eingelegtem Rückwärtsgang das Kamerabild des Rückraums einblenden, sollen kompatibel sein mit 2D- oder 3D-Maschinensteuerungen und deren Grafiken abbilden können, sollen Werte, Statistiken und Diagramme von Telematik und Flottenmanagement verdauen und klar anzeigen können.
Damit ein Display das alles gut bewältigen kann, müssen die Konstrukteure einen Kompromiss finden zwischen der Größe von Breitbildfernseher und Smartphone. Das Ideal liegt irgendwo dazwischen, abhängig von den pro Minute oder Stunde erforderlichen Informationen, Daten und Grafiken, abhängig von der Art und Arbeitsweise der Maschine, abhängig auch von der Größe der Fahrerkabine. Und weil die optimale Lösung manchmal schwer zu finden ist, wählt man gerne mal ein Standard-Display – auch wenn es später im Einsatz zu Problemen führen kann.
Ablesbarkeit und Größe haben nämlich maßgeblichen Einfluss auf den gefühlten Komfort des Fahrers und seine Bediensicherheit. Ob bei starker Sonneneinstrahlung, bei schwachem Licht in dunkler Jahreszeit oder kurzem Seitenblick: Stets muss der Fahrer klar und übersichtlich genau die Informationen und Daten erhalten, die er gerade braucht – aber auch nicht mehr. Muss er bei Sonneneinstrahlung mit einer Hand die Augen abschirmen, wird er zwangsläufig kurz einen Joystick loslassen – mit entsprechenden Folgen für die Arbeitssicherheit.
Joysticks für Multifunktionen müssen blind gehorchen
Joysticks wiederum haben den guten, alten Steuerknüppel längst abgelöst; sie können dank integrierter Tasten, Schalter und Rollen eine Vielzahl an Funktionen übernehmen und den Fahrer von etlichen Armbewegungen und Handgriffen befreien. Bei Baumaschinen muss die Topologie, also die aktuelle Stellung bzw. Position stets „blind“ zu erkennen und zu fühlen sein, damit sich der Fahrer voll und ganz auf Tätigkeit, Umgebung und Arbeitsausrüstung konzentrieren kann. Ein Joystick fungiert als kompakte und übersichtliche 3D-Steuerung, bei der je nach Maschinenart und Aufgabenstellung unterschiedliche Belegungen möglich sind, ob in allen drei Raumachsen oder mit kleinen Tastern und Schaltern für Zusatzfunktionen.
Nun entstammen viele Maschinen einer Klein- oder Kleinstserien oder sind gar eine kundenspezifische Einzelanfertigung. Daher kann oft nicht auf Joysticks aus der Großserienfertigung zurückgegriffen werden. Immer mehr Hersteller installieren bis ins Detail ausgefeilte, auf die jeweiligen Funktionsweisen maßgeschneidert abgestimmte Spezial-Joysticks. Gute Beispiele liefert Caterpillar: Der linke und rechte Joystick sind bei einigen Kettendozern hinsichtlich Formgebung und Funktionstasten völlig unterschiedlich. Eine exklusive Joystick-Technologie der Grader erübrigt immerhin 15 Hebel und sogar das Lenkrad, denn zwei ebenfalls unterschiedliche Joysticks bieten der linken und rechten Hand ein logisches und intuitives Schaltschema. Bei den Mobilbaggern wiederum lässt sich einer der beiden Joysticks optional mit einem integrierten Schiebeschalter ausstatten, damit der Fahrer auf der Baustelle beim häufigen Umsetzen des Baggers im ersten Gang den Joystick nicht mehr loslassen muss.
Ein anderes Beispiel sind die immer beliebteren Tiltrotatoren, die das jeweils angebaute Werkzeug ähnlich wie eine menschliche Hand drehen und neigen können. Die Ansteuerung eines Tiltrotators erfolgt mit elektrischen Tasten oder mit zusätzlichen Fußpedalen, aber auch mit Tasten oder Rollen am Joystick. Um die Bedienung weiter zu optimieren, entwickelte Engcon mit der schwedischen Microprop einen speziellen Joystick mit drei Rollen und sieben Tasten. Damit stehen an beiden Bagger-Joysticks nun sechs Rollen und 14 Tasten zur Verfügung. Durch ein diffiziles Steuersystem können sämtliche Rollen gleichzeitig bedient werden. Die Rollen sind für Daumen, Zeige- und Mittelfinger vorgesehen. In den Joystick ist zudem eine Handstütze integriert, auf der die Hand ruht, damit die Grabbewegungen des Auslegers nicht versehentlich beeinflusst werden. Diese Handstütze ist verstellbar und auf verschiedene Handgrößen einzurichten.
Informationsflut als Sicherheitsrisiko
Letztlich strömen immer mehr Informationen auf Fahrer ein, werden im raschen Wechsel angezeigt und müssen – sofern wichtig – wahrgenommen und interpretiert werden. Zu viele Informationen jedoch, die unentwegt auf den Fahrer einprasseln und verarbeitet werden wollen, sind eher schädlich. Permanentes Multitasking – und nichts anderes verlangen zwei Joysticks, mehrere Displays, Smartphone, Rückfahrkamera, Maschinensteuerung und das Umfeld der Maschine – überfordert irgendwann jeden auch noch so geübten Bediener. Immer wieder stellen Hirnforscher klar, dass niemand tatsächlich zwei Aufgaben, die Aufmerksamkeit erfordern, gleichzeitig erledigen kann. Stattdessen werden dann mehrere rasch wechselnde Tätigkeiten weniger effizient ausführt.
Nachdenklich stimmt auch, was der Deutsche Verkehrssicherheitsrat (DVR) als gefährlichste Ablenkungsfaktoren im Pkw ermittelte: digitale Kommunikation, also SMS, Internet und Navi. Geschätzt wird, dass Ablenkung heute jeden zehnten Verkehrsunfall verursacht. US-Studien beziffern das Unfallsrisiko durch Schreiben und Lesen von Textbotschaften auf das 164-Fache; beim Telefonieren während der Fahrt soll die Ablenkung mit einer Alkoholisierung von 0,8 Promille vergleichbar sein, beim Schreiben von SMS mit den Auswirkungen von 1,1 Promille.
Auch bei Baumaschinen muss wohl hinterfragt werden, ob so manch modernes, blendfreies 7“-Display wirklich so übersichtlich zu bedienen ist, wenn drei Reihen von je sechs Funktionstasten – also insgesamt 18 Tasten – entsprechende Aufmerksamkeit verlangen. Besonders heikel sind nicht eindeutig gekennzeichnete Tastensymbole und oft wechselnde Fahrer mit daher mangelnder Gewöhnung. Nicht alles ist wirklich selbsterklärend. Und aus der Freude, eine Maschine wenigstens bewegen zu können, werden oft Display- oder Tasteneinstellungen wochen- oder monatelang unverändert übernommen. Die Vorteile etwa einer Betriebsartenwahlschaltung sind dann natürlich nichtig.