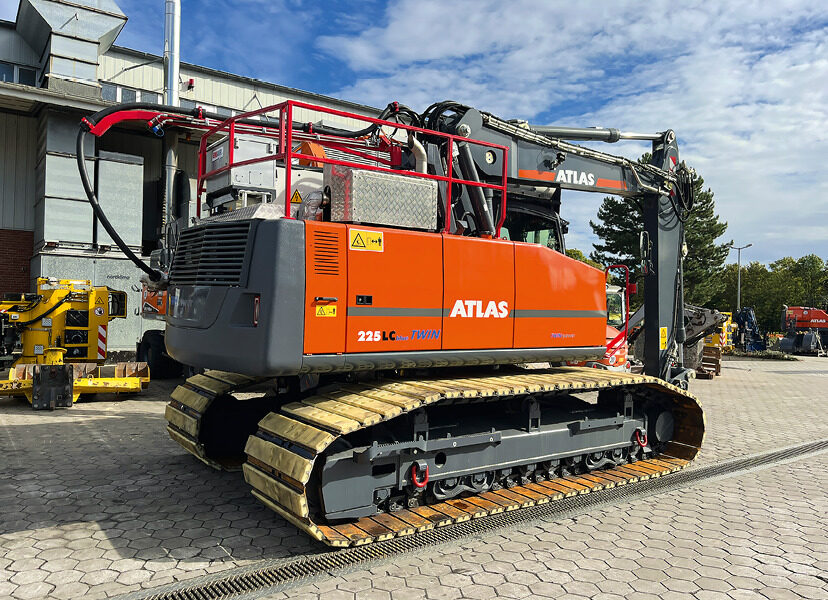
Hoch spezialisierter Atlas-Kettenbagger übernimmt Kampfmittelbergung
Er war wohl der teuerste Bagger, der je auf der Nordbau gezeigt wurde. Aktuell ist der Atlas-Kettenbagger 225 LC Twin Power bei der Sanierung des Dethlinger Teichs in der Lüneburger Heide aktiv. Kurz bevor er in seine lebensfeindliche Umgebung geliefert wurde, konnten wir ihn beim zuständigen Atlas-Händler im Detail begutachten.
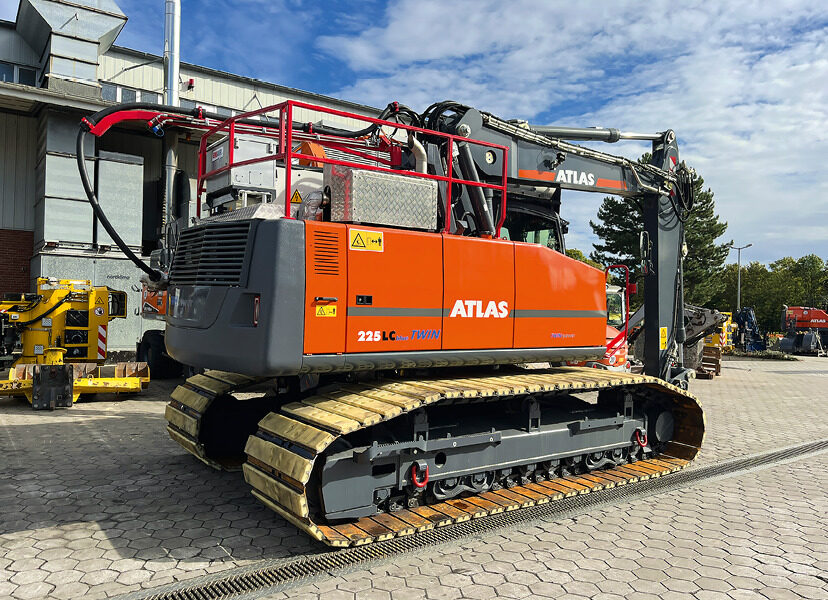
Wie so häufig erlangen kleinere Ortschaften überregionale Bekanntheit erst durch – meist negative – Einzelereignisse. So auch in diesem Fall: Im Dethlinger Teich, einer ehemaligen Kieselgur-Grube, wurde nach dem zweiten Weltkrieg Munition versenkt, die es nicht mehr auf einen Transport zur Verklappung in der Nordsee geschafft hatte. Das Vorhandensein chemischer Kampfstoffe und eine bereits messbare Verunreinigung des Grundwassers erhöhten die Dringlichkeit einer Sanierung.
Zuständige Behörde für die Maßnahme ist der Landkreis, hier der Heidekreis. Er war auch die ausschreibende Stelle für ein Gerät mit diesen besonderen Anforderungen. Erfahrungsgemäß ist die Resonanz bei möglichen Anbietern auf eine derart spezifische Anfrage eher etwas verhalten. Handelt es sich doch um ein Einzelstück, was sowohl technisch als auch kalkulatorisch gewisse Risiken birgt. Also genau die richtige Herausforderung für Ronald Figiel, langjähriger Vertriebsmitarbeiter beim alteingesessenen Baumaschinenhändler Atlas von der Wehl in Lauenbrück. Kontakt zu dem Sanierungsprojekt bestand bereits durch die Lieferung eines gepanzerten Weycor-Radladers.
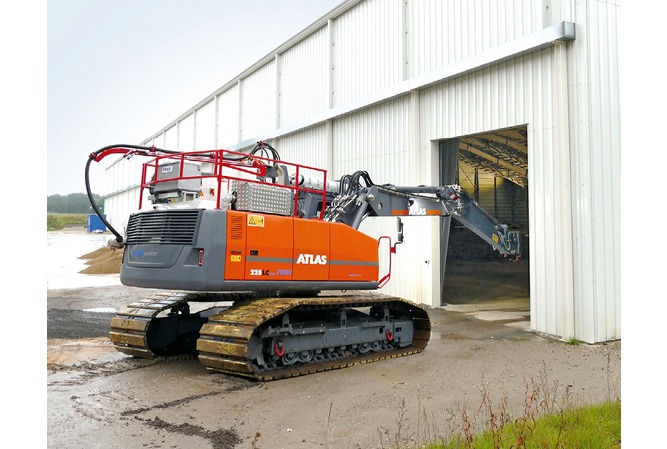
Bei dem gewünschten Kettenbagger war das Lastenheft aber noch um einiges dicker. Zum Schutz der Umgebung wurde über der mittlerweile verfüllten Teichfläche eine freitragende Stahlbau-Halle mit über 10.000 m² Grundfläche errichtet. Um die Luft im Inneren nicht auch noch mit Diesel-Abgasen zu belasten, wurde ein elektrischer Antrieb gefordert – und zwar zusätzlich zum herkömmlichen Verbrennungsmotor.
Also wurde vom Atlas-Werk Ganderkesee ein Bagger Typ 225 LC mit verlängertem Laufwerk (5.000 mm) geliefert. Den Umbau auf den sogenannten Twin-Power-Antrieb übernahm der Atlas-Händler Kern aus Steinach nahe Straubing. Dort werden regelmäßig anspruchsvolle Sonderbauten realisiert, beispielsweise hoch spezialisierte Forstmaschinen auf der Basis von Atlas-Baggern.
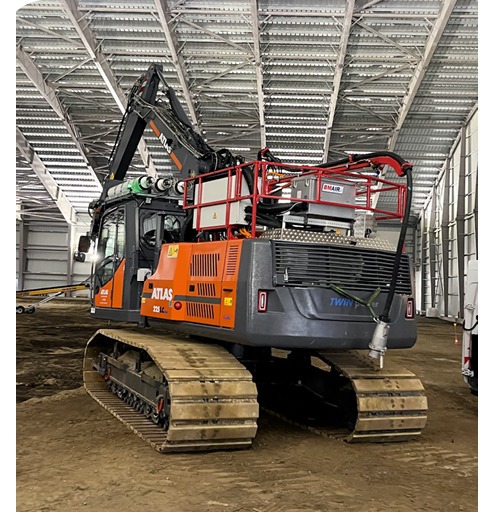
Beim Twin Power bleibt der ursprüngliche Dieselantrieb, mit allen Anforderungen der Stufe V, in vollem Umfang erhalten. Es musste also zusätzlicher Raum für den Elektromotor geschaffen werden. Und dafür wurde das Guss-Heckgewicht ausgeschnitten und um 300 mm zurückversetzt. Der 130 kW starke E-Motor betreibt eine eigene Hydraulikpumpe und verfügt im Vergleich zum Diesel-Aggregat (116 kW) noch über reichlich Reserven. Die Stromversorgung (400 V/400 A) erfolgt durch ein Schleppkabel (5 × 120 mm²), das über einen Schwenkarm auf dem Oberwagen des Baggers nachgeführt wird.
Im höchst unwahrscheinlichen Fall, dass beide Antriebs-Systeme ausfallen, gibt es noch eine dritte Möglichkeit, den Bagger aus einem Gefahrenbereich zu evakuieren: Mittels Schnellkupplungen am Kabel-Schwenkarm kann über die Zusatz-Hydraulik des Radladers hydraulische Leistung eingespeist werden. Durch eine zwischengeschaltete Hydraulikmotor/-pumpen-Einheit, bleiben die beiden Kreisläufe dabei komplett separat.
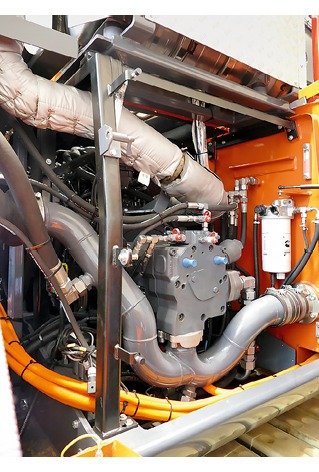
Sicherheit für den Bediener steht bei dieser Sondermaschine ohnehin an erster Stelle. Gefahr droht einerseits durch explodierende Munition, andererseits durch unkontrolliert austretende chemische Kampfstoffe. Die Panzerung der Kabine stammt von der Firma PSV aus Osterholz-Scharmbeck. Deren Kernkompetenz liegt bei der Verstärkung von verschiedensten Fahrzeugen gegen jedwede Einwirkung von außen. Beim Atlas 225 bedeutet dies, neben der Verwendung von robusten Stahlplatten, den Einbau von Panzerglas mit einer Stärke bis 56 mm. Damit entspricht die Schutzstufe der Nato-Kategorie Stanag Level II, was nur eine Stufe unter der Panzerung des Leopard II liegt.
Durch das erhebliche Gewicht ist die Tür nicht mehr von Hand zu bedienen, sie hat deshalb einen elektrischen Antrieb. Kommt es hier zu einem Defekt, ist die Heckscheibe leicht demontierbar und wird zum Fluchtweg. Ein Nebeneffekt der großen Glasstärken ist, dass die übliche Defroster-Düse der Kabinenheizung so gut wie wirkungslos ist. Aus diesem Grund ist das Panzerglas mit einer integrierten Scheibenheizung versehen.
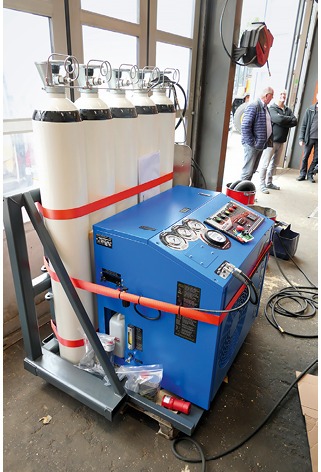
Im Normalbetrieb wird die Überdruck-Kabine durch eine Schutzbelüftungsanlage der Firma BM Air versorgt. Sobald jedoch der Phosgen-Sensor von Dräger auf dem Oberwagen eine Grenzwert-Überschreitung meldet, wird die Kabinenbelüftung auf Umluft umgestellt. Die Versorgung mit Atemluft übernehmen dann drei Pressluftflaschen auf dem Kabinendach. Deren Inhalt ist für 45 Minuten ausgelegt und ermöglicht ein sicheres Entfernen aus dem Gefahrenbereich.
Zum Lieferumfang gehört ebenso ein Kompressor zum Nachfüllen der Druckflaschen. Dieses System wird üblicherweise für den Einsatz von Tauchern verwendet und liefert entsprechend ölfreie, saubere Atemluft. Auf ein Radio in der Kabine wurde bewusst verzichtet, nichts soll die Aufmerksamkeit des Bedieners beeinträchtigen. Es besteht lediglich Funkkontakt zum Radlader und dem Leitstand, von dem auch sämtliche Arbeiten per hochauflösendem Kamerabild verfolgt werden.
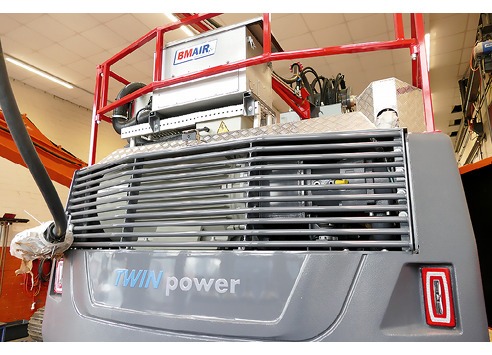
Millionen-Maschine mit diffizilem Innenleben
Als Folge der gesamten Umrüstungen ist das Einsatzgewicht des Baggers von zirka 23 auf knapp 30 t gestiegen, und der Preis hat zuletzt noch die Grenze zur Siebenstelligkeit gerissen. Eine Voraussetzung zum Gelingen dieses wohl weltweit einzigartigen Projekts war die außergewöhnlich gute Vernetzung der erfahrenen Atlas-Händler untereinander und mit dem Werk in Norddeutschland. Bei einem derart tiefen Eingriff ins Bagger-Innenleben ist der Zugang zu allen relevanten technischen Informationen essenziell, kann doch heutzutage das unbedarfte Durchkneifen eines Kabels zu unüberschaubaren Folgen führen.
Vor Kurzem nun wurde mit dem eigentlichen Freilegen und Bergen der Kampfmittel begonnen. Neben den üblichen Anbaugeräten wie Löffel und Greifer, die per Oilquick-Schnellwechsler getauscht werden, wird hauptsächlich eine hydraulisch angetriebene Saugbox zum Einsatz kommen. Gemeinsam mit dem Bodenpersonal, das immer aus zwei Kampfmittel-Spezialisten in Körper-Vollschutz besteht, kann die Munition damit besonders schonend freigelegt werden.
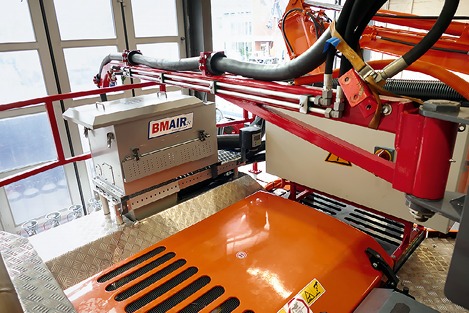
Sie wird anschließend von Hand geborgen und nach eingehender Untersuchung beim nahegelegenen Entsorgungsfachbetrieb GEKA in Munster einer Hochtemperatur-Verbrennung zugeführt. Die Dauer der Sanierung wird auf fünf bis sieben Jahre geschätzt, wofür derzeit 85 Mio. Euro veranschlagt werden. Dabei wird sich der Bagger stufenweise in eine Tiefe bis 15 m vorarbeiten, bis die giftige Hinterlassenschaft restlos beseitigt ist.