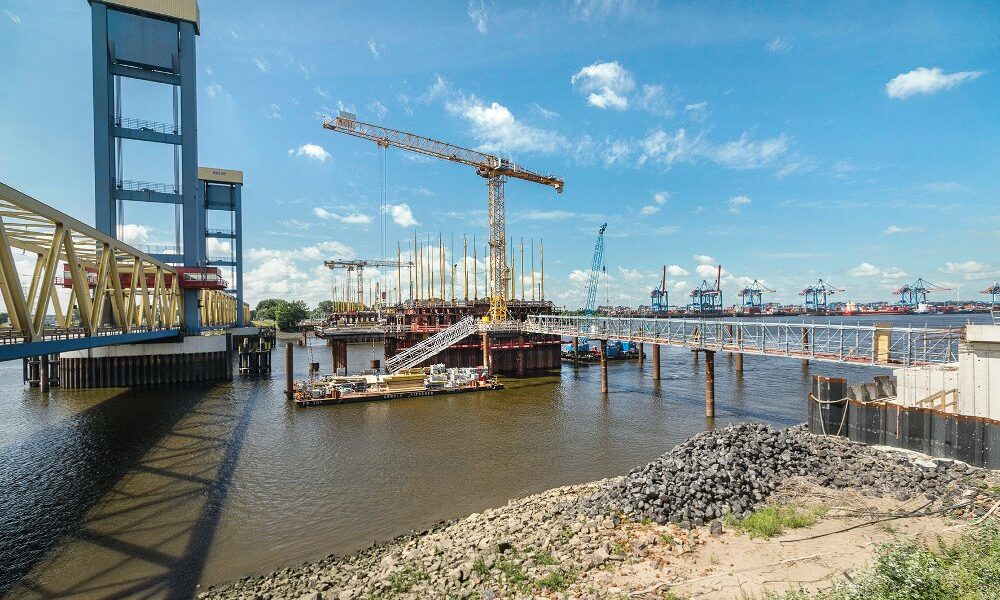
Invertierter Brückenbau an Deutschlands größter Hubbrücke
Für den Bau der Neuen Bahnbrücke Kattwyk entwickelten der Schalungsspezialist Doka und das Bau-Unternehmen Max Bögl eine abgehängte Pfeilerschalung. Das heißt, dass die Brückenpfeiler nicht von unten nach oben, sondern von oben nach unten gebaut werden.
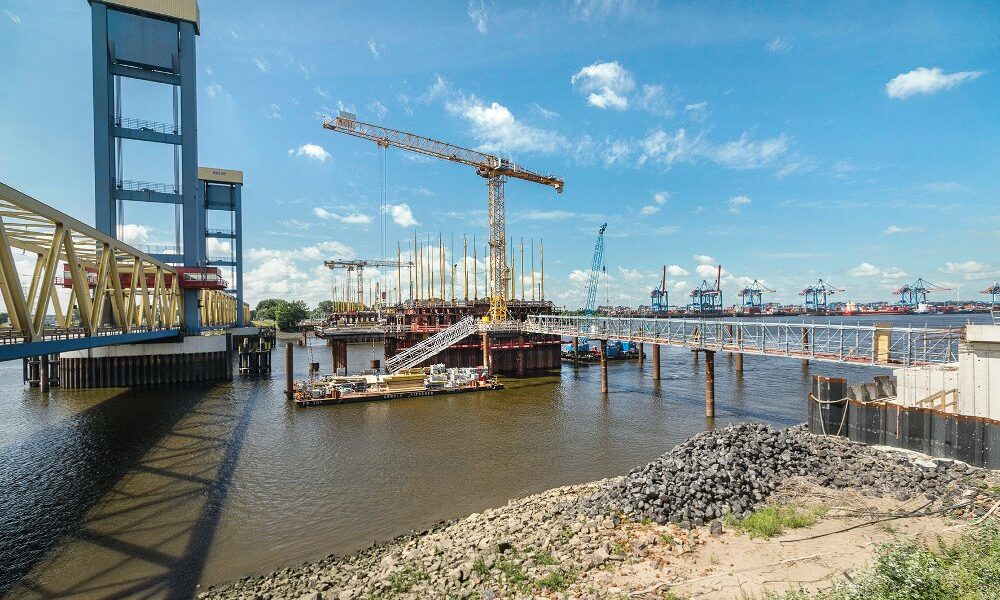
Im Jahr 2020 werden die ersten Züge über die neue Brücke rollen. Mit einer Durchfahrtsbreite von 108 m löst die neue die alte Kattwykbrücke (96 m) als größte Hubbrücke Deutschlands ab und zählt dann zu den größten weltweit. Sie soll den Verkehrsfluss über die Süderelbe in Hamburg verbessern. Die alte Kattwykbrücke aus dem Jahr 1973 ist wichtiger Knotenpunkt für den industriellen Verkehr der Hansestadt und führt sowohl den Bahn- als auch den Straßenverkehr über das Gewässer. Für den Schiffsverkehr wird die 290 m lange Brücke zeitweise gesperrt und das mittlere Hubteil nach oben gefahren. Durch die gemeinsame Nutzung für Zug, Auto und Schiff entstehen für den Straßenverkehr bis zu sieben Stunden Wartezeit pro Tag.
Um die Nutzung für Bahn- und Straßenverkehr zu entflechten und die alte Brücke vom schweren Güterverkehr zu entlasten, wird die parallel zur Kattwykbrücke entstehende Neue Bahnbrücke Kattwyk ausschließlich für den Schienenverkehr genutzt werden, während über die alte Kattwykbrücke weiterhin der Straßenverkehr rollt.
Zwei Brückenpfeiler sind zu errichten, deren Bau im Wasser erfolgt. „Wir haben es mit sehr beengten Platzverhältnissen zu tun. Das Einheben der Schalung konnten wir zwar per Kran meistern, doch die Bewehrung musste per Hand eingebracht und die Schalung über Kettenzüge nach oben und unten bewegt werden“, erklärt der bei Max Bögl zuständige Polier. Die Brückenpfeiler entstehen in geschlossenen Spundwandkästen, deren Baugruben aus statischen Gründen nur in einer bestimmten Größe hergestellt werden konnten. So müssen beim Abtragen der Lasten die Kräfte berücksichtigt werden, die zum einen aus dem aufgehängten Senkkasten (rund 1.230 t) und zum anderen durch den Wasser- und Eisdruck entstehen. Aufgrund dieser statischen Bedingungen, aber auch wegen der Gründungstiefe von minus 30 m NN und etwa 19 m unterhalb der Elbsohle können die Pfeiler nicht in konventioneller Weise hergestellt werden. Anstatt die Tiefgründung mit Fundament zu errichten und von dort nach oben zu bauen, entwickelte Doka zusammen mit Bögl ein Schalungskonzept, das den konventionellen Pfeilerbau auf den Kopf stellt: eine abgehängte Pfeilerschalung.
Dazu wird die Schalung samt Schachtbühnen komplett frei am Stahlbau aus eng gestaffelten, auf den Spundwänden aufliegenden Tragprofilen aufgehängt. Weil die Tragprofile aber nur eine bestimmte Last abtragen können, müssen Schalung und Betonbau ab einem gewissen Bauabschnitt (BA6) entkoppelt werden. Auf diese Weise wird der Betonkörper abschnittsweise in 5 m hohen Betoniertakten hergestellt und nach dem Ausschalen in den Elbuntergrund abgesenkt beziehungsweise eingespült.
Bis zum Aufsetzen auf der Elbsohle erfolgt das Absenken der Betonierabschnitte mit einer Absenkvorrichtung aus 24 hydraulischen Hohlkolbenzylindern und Pressen. Daran sind die betonierten Pfeilerabschnitte mit insgesamt 24 Gewindestäben (d = 75 mm) aufgehängt. Ist eine ausreichende Einbindetiefe in den Elbuntergrund erreicht, werden die Gewindestäbe abgetrennt und die Absenkvorrichtung zurückgebaut. Danach ändert sich der Absenkmechanismus: Unter Druckluft werden der Strompfeiler mit Sand und Wasser ballastiert sowie der Boden entfernt – und zwar mit Hilfe unterhalb des Strompfeilers im Caisson angeordneter und ferngesteuerter Wasserkanonen und eines Baggerarms. Durch den so kontrolliert erzeugten Grundbruch sinkt der Strompfeiler ab.
Bei einem solchen Projekt sind Schalungsplanung und enge Abstimmung extrem wichtig. „Doka hat uns die abgehängte Pfeilerschalung als Gesamtkonzept zur Verfügung gestellt. Zusätzlich profitieren wir von deren Fertigservice, der uns die einzelnen Schalungselemente vorgefertigt auf die Baustelle liefert“, so Bauleiter Fabian Böse. Aufgrund der örtlichen Randbedingungen mit Pfeilerbau im Wasser, keinem Kran nach der Erstmontage und wenig Lagerfläche am Ufer gab es auch logistische Herausforderungen. Dafür stand dem Bau-Unternehmen ein Doka-Richtmeister zur Seite, mit dem das Montagekonzept erarbeitet und das Ganze vor Ort montiert wurde.
Am Ende wird jeder der beiden Pfeiler eine Höhe von etwa 39 m haben und rund 19 m in den Elbuntergrund einbinden. Aus statischen Gründen müssen jeweils über 1.000 t Bewehrung in den Pfeilern verbaut werden – für den Fall einer Maximalbelastung. Das wäre dann der Fall, wenn zwei Güterzüge von je 750 m Länge und über 6.000 t Gewicht gleichzeitig auf der Brücke eine Vollbremsung vornehmen müssen.