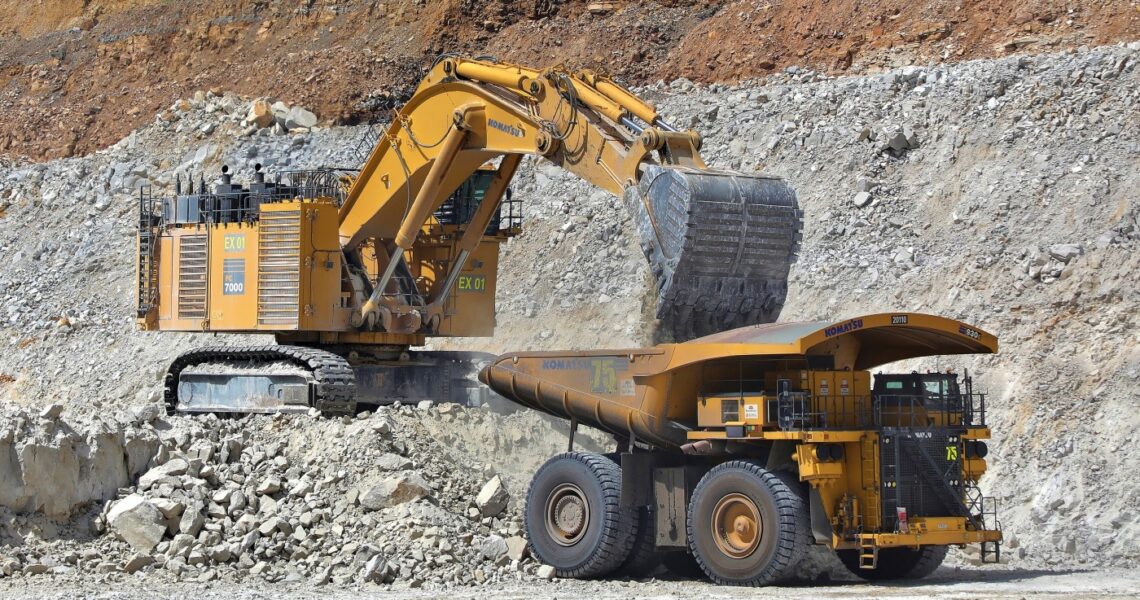
Komatsu-Großbagger kommen aus Düsseldorf
Ein Vierteljahrhundert nachdem Komatsu die traditionsreiche Demag-Baggerfabrik in Düsseldorf-Benrath übernommen hat, werden dort immer noch Großbagger für den Weltmarkt produziert. Und damit das weiterhin so bleibt, wird kontinuierlich in den Standort investiert.
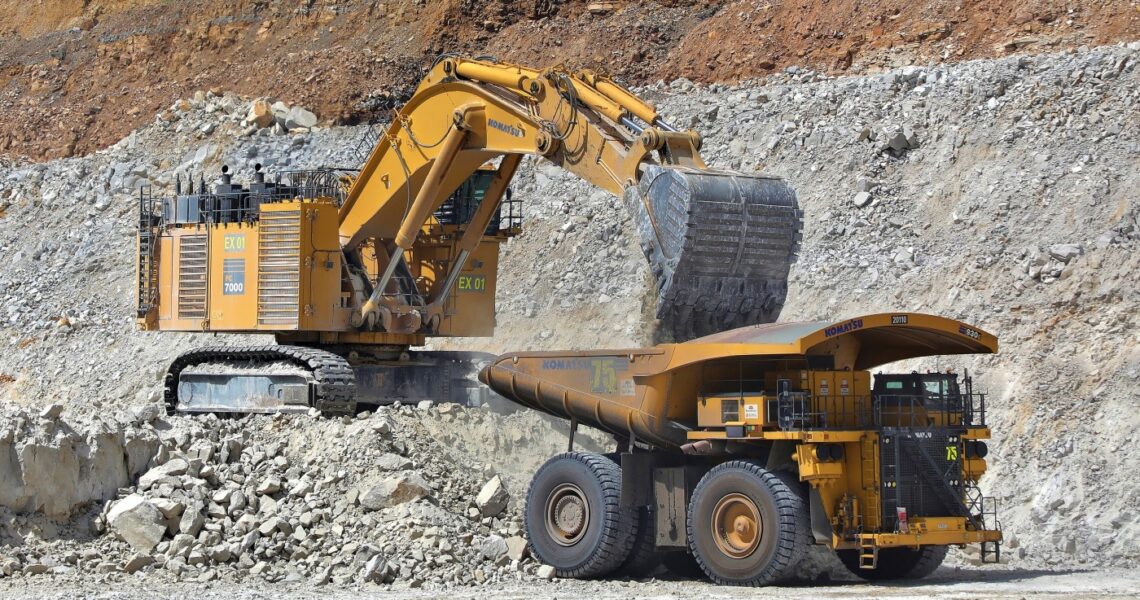
Der Stadtteil Benrath versteht sich gerne abgeschlossenes Biotop im mondänen Düsseldorf. Man verweist auf eine reiche Tradition, wobei die meisten sicher eher das barocke Schloss Benrath im Sinn haben. Es gibt hier jedoch auch eine bedeutende industrielle Historie, und daran hatte die 1939 in Betrieb genommene Demag-Baggerfabrik stets einen erheblichen Anteil. Dass hinter der langen Mauer an der Forststraße auch heute noch Produkte von Weltrang entstehen dürfte den meisten Anwohnern allerdings verborgen bleiben.
Als sich Komatsu in den 1990er-Jahren zunächst in Form eines Joint-Ventures in die Düsseldorfer Fertigung eingebracht hat, hatten Demag-Großbagger bereits ihren festen Platz in der internationalen Mining-Industrie. Das Benrather Werk verfügte über einen reichen Erfahrungsschatz in der Herstellung von schweren Stahlbauteilen, Laufwerkskomponenten und Hydraulikzylindern. Die Japaner hatten schnell erkannt, dass sie langfristig den größten Nutzen aus ihrem Invest ziehen würden, wenn sie das vorhandene Know-how und Fachpersonal am Standort belassen und weiter entwickeln. Also wurde kräftig investiert, sowohl in Infrastruktur als auch in Produktionsmittel.
Die Mining Division von Komatsu Germany bietet in Benrath gut 900 Beschäftigten, die teilweise mehrschichtig arbeiten, einen Arbeitsplatz. Als großer Vorteil erweist sich die räumliche Konzentration von Konstruktion, Entwicklung und Fertigung: Sollten einmal Fragen auftreten, können sie auf kurzem Dienstweg geklärt werden. Das Gleiche gilt für langjährige Zulieferer von Komponenten, mit denen es eine enge Zusammenarbeit gibt.
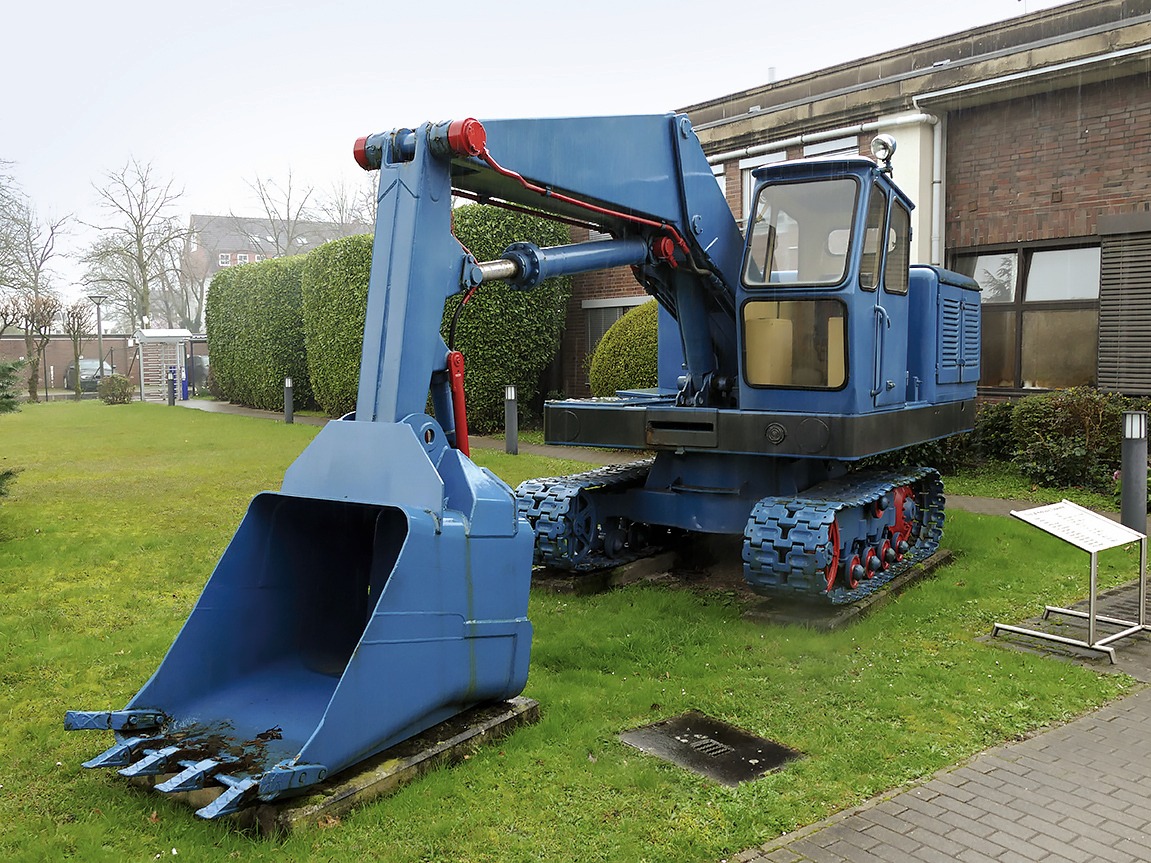
Zu den Kernkompetenzen des Düsseldorfer Werks gehörte schon immer ein äußerst solider Stahlbau. Nicht rein zufällig sind heute noch Demag-Großbagger im Einsatz, die teilweise Betriebsstunden in sechsstelliger Höhe abgeleistet haben. Die hochbelasteten Laufwerkskomponenten sind durchweg Eigenkonstruktionen, da es in diesen Größenordnungen bei den Herstellern von System-Traktorketten nichts mehr gibt. Die dafür erforderlichen Stahlgussteile werden nach Werksvorgaben von langjährigen Partnern zugeliefert. Die Wärmebehandlung erfolgt dann wieder komplett im Haus, da das richtige Verhältnis von Oberflächenhärte und Zähigkeit einen ganz entscheidenden Einfluss auf die Lebensdauer hat. Gerade beim Induktionshärten von Bodenplatten, Laufrollen, Turassen und Leiträdern hat sich Komatsu große Expertise erworben.
Die Fertigungstiefe von etwa 70 Prozent ist schon sehr beeindruckend, ist aber auch teilweise alternativlos: Die hier vorgehaltenen Werkzeugmaschinen wird kaum ein Zulieferer in seinem Angebot haben. Mehrachsige Bohr- und Fräswerke, die Werkstücke bis 120 t Gewicht und etlichen Metern Ausdehnung aufnehmen können, beherrschen die 2.250 m² große Abteilung Mechanische Bearbeitung Großbauteile. Die Herstellung aller Hydraulikzylinder erfolgt – bis auf den Hartchrom-Auftrag – ebenso im Haus. Für deren Montage gibt es spezielle Arbeitsplätze, bei denen die senkrecht stehenden, lang bauenden Komponenten unterflur versenkt werden können, was ein ergonomisches Arbeiten ermöglicht.
Die erste Ölbefüllung und Druckprobe erfolgt in einem gekapselten Prüfstand, um Gefahren für die Beschäftigten bei eventuellen Leckagen auszuschließen. Und auch die kompletten Kabelbäume werden in der hauseigenen Elektrowerkstatt konfektioniert. All diese Maßnahmen garantieren Komatsu die maximale Kontrolle über sämtliche relevanten Komponenten ihrer Großbagger. Zugleich stellt man auf diese Weise sicher, dass über Jahre erlangtes Know-how auch am Standort verbleibt.
Bei der Ausstattung der Bagger mit Dieselantrieb profitiert Komatsu von der bewährten Partnerschaft mit dem Motorenhersteller Cummins, um sicher stellen zu können, dass die Aggregate optimal auf diesen speziellen Einsatzfall ausgelegt sind. Der alternativ erhältliche Elektroantrieb ist beileibe nicht der aktuellen Diskussion entsprungen: Der erste Mining-Bagger mit E-Antrieb aus Benrath, ein DEMAG H 241, wurde bereits 1980 an eine texanische Kohlemine geliefert. Das war damals eigentlich keine große Sache, da die großen Bergbaubetriebe bereits über eine entsprechende Infrastruktur verfügten: Die vorher verwendeten Hochlöffel-Seilbagger wurden ebenfalls ausschließlich elektrisch mittels Schleppkabel betrieben.
Da alle in Düsseldorf gefertigten Bagger das Werk zerlegt als Baugruppen verlassen, erfolgt nur eine Teilmontage. Die Oberwagen werden einschließlich Antrieb, Hydraulik und Steuerstand komplett montiert; anschließend können auf einem Prüfstand Betriebsbelastungen simuliert und erste Systemeinstellungen vorgenommen werden. Die einsatzfähige Maschine mit Arbeitsausrüstung und Unterwagen wird dann erstmals beim Kunden Ort zusammengefügt. Die heutigen Fertigungstechniken und Möglichkeiten zur Qualitätssicherung stellen dabei sicher, dass alle Teile zueinander passen und es bei der Erstmontage beispielsweise mitten in den Anden nicht zu schweißtreibenden Überraschungen kommt. Lediglich Prototypen werden noch komplett montiert und ersten Funktionstests unterzogen.
Einen neuen Service gibt es im Benrather Werk auch: die Überholung von elektrischen Antriebskomponenten. Die Radnaben-Elektromotoren der diesel-elektrischen Minen-Muldenkipper können gereinigt, instandgesetzt und deren Leistungswerte auf einem Prüfstand sichergestellt werden. Der Transportweg von Austausch-Komponenten, insbesondere für nordeuropäische Kunden, verringert sich so entscheidend. Das moderne Ersatzteilzentrum wurde komplett neu errichtet und stellt – in Kooperation mit einem Logistikpartner, der in Werksnähe über zusätzliche Lagerkapazitäten verfügt – die Betriebsbereitschaft der weltweit tätigen Großbagger sicher.
Wer ein wenig wehmütig über das Verschwinden von traditionsreichen deutschen Baggerherstellern sinniert, den trösten eventuell Fakten: Seit Komatsu 1999 die volle Verantwortung für den Standort in Düsseldorf-Benrath übernommen hat, wurde allein in die Liegenschaft mehr investiert als all die Jahrzehnte davor. Komatsu hat die Großbagger in ein komplettes Portfolio an Gewinnungsgeräten für den Unter- und Übertage-Bergbau integriert und damit als Systemanbieter eine sehr starke Position am Markt. Und vielleicht das Wichtigste: Die Produktion erfolgt immer noch hier in der Landeshauptstadt Nordrhein-Westfalens. Dass dies auch so bleiben soll, bekräftigt das Unternehmen mit Plänen, die bereits in der Schublade liegen. So soll eine der über 80 Jahre alten Hallen durch eine zeitgemäße ersetzt werden, verbunden mit digitalisierten Produktionsmitteln auf aktuellstem Stand.