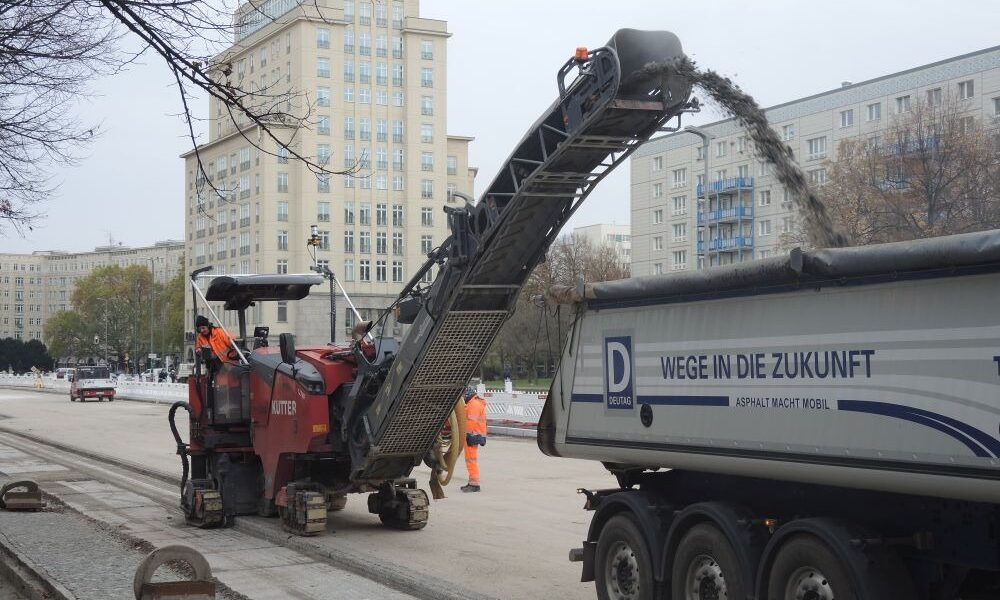
Kompaktfräse profiliert Betondecke mit 3D-Nivellierung
Auf der Berliner Karl-Marx-Allee hat Kutter aus Memmingen das diffizile Profil einer Pendelrinne in eine Betonfläche eingefräst. Weil unter der Straße eine U-Bahn-Linie verläuft, kam für die Maßnahme keine Großfräse in Frage. Die Lösung: 3D-Fräsen mit einem Kompaktgerät mit 1 m Fräsbreite, sodass das Niederschlagswasser sicher abgeleitet werden kann.
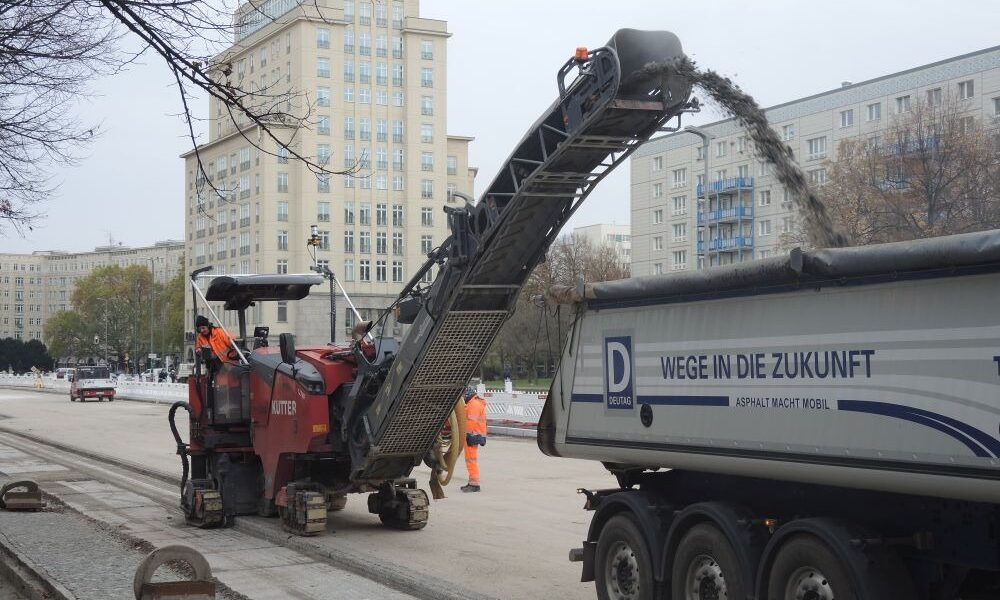
Die Karl-Marx-Allee, eine bis zu 72,50 m breite, geschichtsträchtige Prachtstraße im Herzen Berlins, wird seit Sommer 2018 in mehreren Schritten neugestaltet. Künftig wird es dort weniger Platz für Autos geben, dafür breite Radwege sowie attraktive Gehwege und Plätze. Dazu wurden nach dem Abtrag der bituminösen Fahrbahnbeläge die Regenabläufe und die Bordanlage neu gesetzt.
Bautechnisch herausfordernd war dann der nächste Schritt: die Profilierung der Betondecke unter dem Asphalt. Sie sollte, um später den Abfluss des Regenwassers sicherzustellen, auf gut 800 m Länge und 5,75 m Breite das Profil einer Pendelrinne erhalten. Die Planung sah vor, dass das Gefälle in Abständen von 3 bis 5 m zwischen 2,5 und 3,0 Prozent variiert. Auf den verbleibenden 9,25 m Breite der Fahrbahn sollte das Profil eine Querneigung von 2,5 Prozent von der Mitte zum Fahrbahnrand aufweisen. Aus dieser Geometrie ergab sich eine ständig wechselnde Frästiefe zwischen 0 und 12 cm. Und weil unter Teilen der Karl-Marx-Allee die U-Bahn verläuft, kam auf rund drei Vierteln des Baufelds wegen entsprechender Lastbeschränkungen der Einsatz von Großfräsen nicht in Frage.
Für die Auftraggeber, die Senatsverwaltung für Umwelt, Verkehr und Klimaschutz war es zudem ausgesprochen wichtig, dass das Profil exakt abgebildet wird, denn die Karl-Marx-Allee weist praktisch keine Längsneigung auf. Deswegen ist die gezielte Ableitung des Regenwassers durch ein ausreichendes Gefälle zu den Außenrändern essentiell für eine sichere Verkehrsführung. Also entwickelte das Team des Frässpezialisten Kutter mit dem Hauptauftragnehmer Matthäi ein Konzept für die präzise Profilierung des Betons. Man wählte dafür eine Kompaktfräse mit 1 m Fräsbreite, ausgestattet mit einem 3D-Nivelliersystem mit Totalstation. Üblicherweise kommen für das 3D-Fräsen nur Großgeräte mit mindestens 2 m Fräsbreite zum Einsatz.
Das Prinzip beim 3D-Fräsen mit Totalstation: Zunächst erstellt der Auftraggeber ein digitales Geländemodell. Darin wird für jeden Punkt festgelegt, wo die Oberkante der späteren Fahrbahndecke liegen soll. Daraus ermittelt der Hauptauftragnehmer dann durch Abzug der Schichtdicken die Werte für die Lage der Fräsfläche. Die entsprechenden Daten werden auf einen Systemcomputer der Kaltfräse übertragen – damit kennt die Fräse für jeden Punkt die Soll-Höhe der Fräsfläche. Während des Fräsens verfolgt dann eine Totalstation ein Prisma an der Kaltfräse. Es dient als Referenz für die Höhe der gefrästen Fläche. Die Totalstation ermittelt kontinuierlich die Lage des Prismas im Raum und funkt die Messdaten an den Systemcomputer auf der Fräse. Dort wird die gemessene Höhe mit den Sollwerten verglichen. Die Maschine reagiert bei Abweichungen in Sekundenbruchteilen und passt die Frästiefe an.
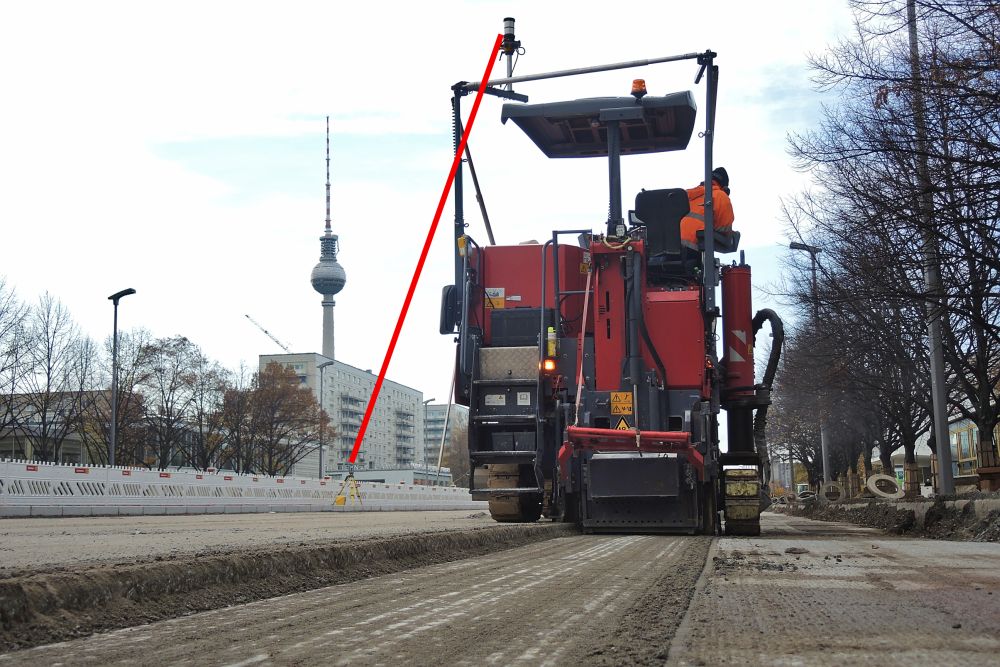
Mit dieser Methode konnte die diffizile Fräsaufgabe in nur einer Woche gelöst werden. „Die Hochpunkte lagen im Mittel etwa 10 m auseinander. Das heißt, die Frästiefe änderte sich kontinuierlich, aber mit der 3D-Fräse konnten wir das Profil exakt wie geplant herstellen“, berichtet Matthias Dreer, Bauleiter bei Kutter. „Die Maschine reagiert äußerst schnell. So betrugen die Abweichungen vom Geländemodell höchstens 3 mm vom Sollwert. Und das in der Totalen – nicht nur beim Check mit der 4-m-Latte.“ Damit haben die Frässpezialisten die geforderte Genauigkeit von ± 5 mm gemäß ZTV souverän unterboten und beste Voraussetzungen für den Aufbau des Asphaltüberbaus geschaffen. Er konnte anschließend ohne aufwendige Nivellierung und ohne Ausgleichsschichten mit konstanter Schichtdicke zügig eingebaut werden.
Zudem ist diese Methode auch wirtschaftlich, obwohl das 3D-Fräsen aufwendiger ist als das herkömmliche Kopierfräsen. Dafür sinken aber die Gesamtprojektkosten, denn die Investition in die Erstellung eines digitalen Geländemodells im Vorfeld und die messtechnische Begleitung eines Vermessungsteams werden mehr als kompensiert – weil das Einbringen von Ausgleichsschichten entfällt und der Bauablauf sich verkürzt.
Standpunkt
Roland Schmid Leiter Fräsabteilung, Kutter, Memmingen
„Beim Erstellen neuer Profile arbeiten wir seit fast einem Jahrzehnt äußerst erfolgreich mit der 3D-Nivellierung und haben mittlerweile verschiedene Systeme ausprobiert. Die Variante mit Totalstation hat sich bei unterschiedlichsten Aufgabestellungen bestens bewährt. Deshalb waren wir sicher, auch das Projekt in Berlin-Mitte auf diese Weise erfolgreich abzuwickeln.“