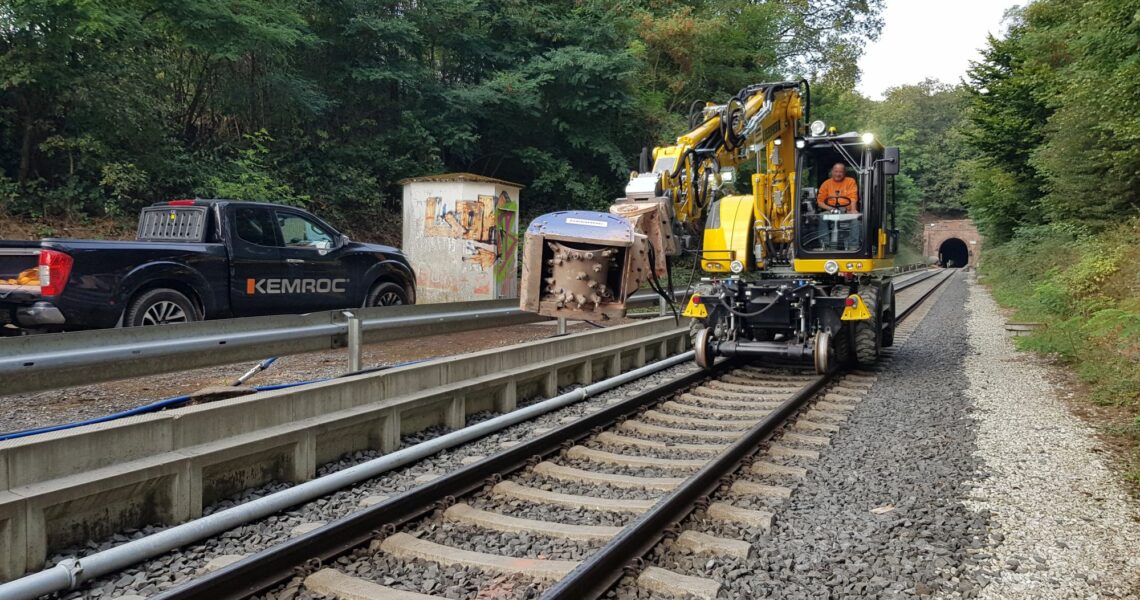
Tunnelsanierung mit Kemroc-Flächenfräse
Bei der Sanierung des Hasselborner Tunnels nutzte das Unternehmen Baresel eine bislang ungewöhnliche Methode. Das Tunnelgewölbe sollte partiell abgefräst werden, um die betroffenen Stellen anschließend für einen lokalen Neuaufbau der Tunnelschale mit Spritzbeton und Kunststoffabdichtungen auszukleiden. Mit einer Kemroc-Flächenfräse EX 45 HD konnte Baresel die Fräsarbeiten effizient und präzise ausführen.
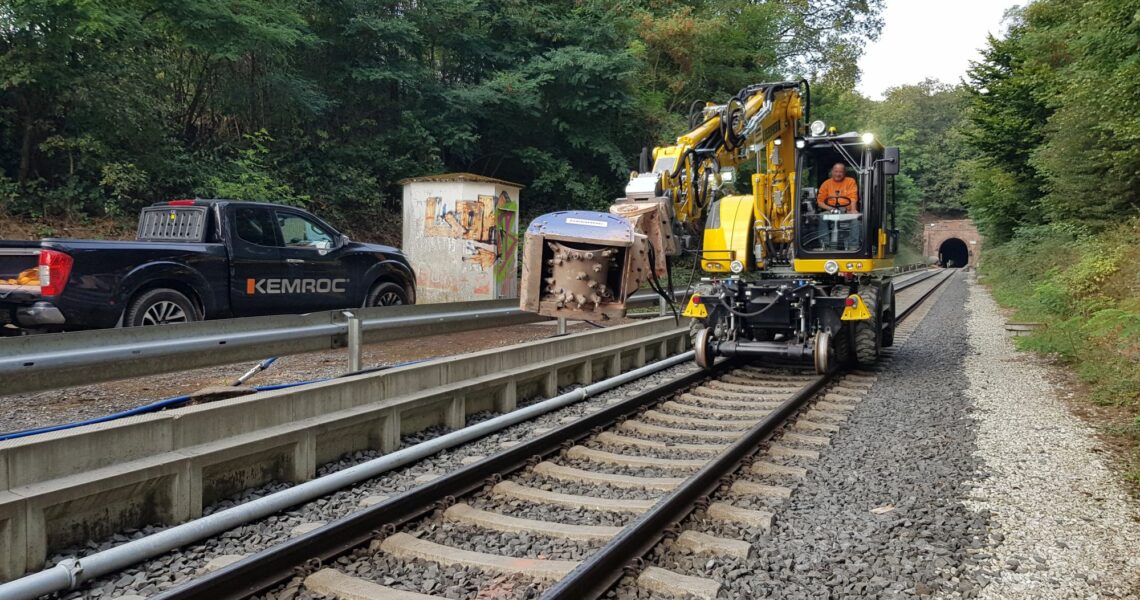
Der 1.300 m lange Hasselborner Tunnel in Mittelhessen hat eine lange Geschichte. Er wurde zwischen 1910 und 1912 aufgefahren und unterhalb des Kämpfers aus Naturstein sowie im Bereich des Gewölbes von 9 bis 15 Uhr aus Ziegelmauerwerk erbaut. Heute verbindet der einspurige, nicht elektrifizierte Eisenbahntunnel im Verlauf der Taunusbahn die Ortschaften Grävenwiesbach und Hasselborn westlich von Frankfurt am Main. Nach rund hundert Jahren war nun eine Sanierung der Tunnelauskleidung notwendig, um das Eindringen von Wasser zu verringern, die Betriebssicherheit zu erhöhen und die Dauerhaftigkeit für weitere 50 Jahre zu gewährleisten. Den Zuschlag für diese Arbeiten erhielt das Bauunternehmen Baresel aus Leinfelden-Echterdingen, das sich mit anspruchsvollen Tunnelbau- und Sanierungsprojekten einen Namen gemacht hat.
Neben verschiedenen Abbruch-, Bohr-, Spritzbeton- und Verankerungsarbeiten mussten die Spezialisten von Baresel teilweise das Tunnelgewölbe abfräsen, um die betroffenen Stellen danach mit einer neuen Tunnelschale inklusive Kunststoffdichtungsbahnen (KDB) auszukleiden. Eine Kemroc-Flächenfräse wurde als dafür am besten geeignet in die Kalkulation einbezogen. Dabei ermittelten das Baresel-Team Maschinentechnik Tunnelbau (MTT) unter Leitung von Josef Galster sowie das Kemroc-Team um Geschäftsführer Klaus Ertmer den richtigen Flächenfräsen-Typ für den von Baresel vorgesehenen Zweiwegebagger. Die Wahl fiel schließlich auf die Flächenfräse EX 45 HD, denn sie versprach einen hohen Fräsfortschritt sowie geringe Erschütterungen am Bagger und im Grundgebirge.
Kemroc-Flächenfräsen der Serie EX (Exactor) dienen unter anderem zum Ausbessern von Asphaltflächen oder zum Abfräsen von Beton und Estrich. In acht Baugrößen sind sie für Bagger und Trägergeräte von 1 bis 23 t verfügbar. Je nach zu fräsendem Material können sie mit unterschiedlichen Frästrommeln und Werkzeugen bestückt werden. Die wahlweise mechanisch oder hydraulisch justierbare Tiefeneinstellung ermöglicht ein millimetergenaues Fräsen bis – je nach Modell – 190 mm Eindringtiefe. Im Hasselborner Tunnel sollte ziemlich gleichmäßig 25 bis 30 cm tief ins Ziegelmauerwerk gefräst werden, deswegen wählte man die Variante mit mechanisch justierbarer Tiefeneinstellung.
Grundsätzlich kann der Exactor in jeder räumlichen Position betrieben werden – sowohl horizontal als auch vertikal oder sogar über Kopf wie etwa im Tunnelbau. Jedoch war die räumliche Enge im eingleisigen Hasselborner Tunnel eine gewisse Herausforderung: Der Zweiwegebagger kann in diesem engen Tunnel mit rund 5 m lichter Weite und 5,20 m lichter Höhe nicht drehen und damit auch den Anstellwinkel der Anbaufräse am Tunnelgewölbe nur geringfügig verändern. Darum wurde die Flächenfräse an einen Tiltrotator montiert. So kann der Baggerfahrer mit wenigen Joystick-Bewegungen die Fräse in den passenden Anstellwinkel an der Tunnelschalung bringen. Im konkreten Einsatz setzt der Maschinist die Fräse an einer bestimmten Stelle des Gewölbes an, fräst bis zur eingestellten Tiefe ins Ziegelmauerwerk und fährt dann axial fünf Meter weit voran. Das abgefräste Material fällt dabei auf einen bereitgestellten Plattformwagen. Auf diese Weise war neben einem gleichmäßigen Fräsbild im Tunnelgewölbe auch der Abtransport des Fräsguts eine saubere Sache. Laut Baresel MTT mussten nur die aus hartem, gemauertem Naturstein bestehenden Bereiche unterhalb des Kämpfers herkömmlich mit einem Hydraulikhammer bearbeitet werden.
Zugleich sei man mit der EX 45 HD exakt im verbindlichen, eng gesteckten Zeitrahmen der Betriebs- und Bauanweisung geblieben. Noch während dieses Einsatzes übernahm die Baresel MTT eine zweite Kemroc-Flächenfräse in ihr Maschinenarsenal, um sie bei ganz ähnlichen Sanierungsprojekten in den Tunneln Kalmut und Talberg bei Boppard am Rhein einzusetzen. Hier mussten die lnnenschalen aus Ziegelmauerwerk ebenfalls in einer vordefinierten Tiefe teilweise abgebrochen werden. Gegenüber herkömmlichen Verfahren wie Schneiden und Hämmern oder anstelle der herkömmlichen Verwendung von Querschneidkopffräsen – so resümiert man bei der Baresel MTT – habe sich die Arbeit mit der Flächenfräse in weichen bis mittelharten Materialien als rationelles, exaktes und gebirgsschonendes Verfahren herausgestellt.