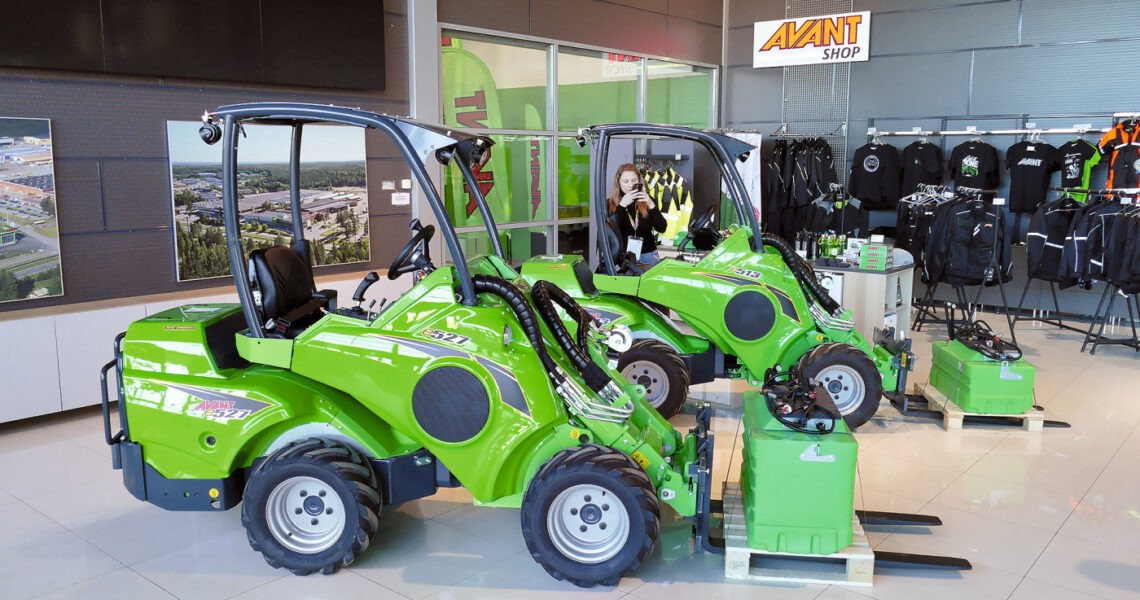
Zwei neue Akku-Multifunktionslader von Avant
Am Stammsitz von Avant in Finnland lief Anfang des Jahres die Produktion von zwei Akku-Ladern an. Dafür wurde gleichzeitig eine eigene Batterie-Fertigung in Betrieb genommen. Der bd-Baumaschinendienst hat sich vor Ort umgesehen und die Maschinen ausprobiert.
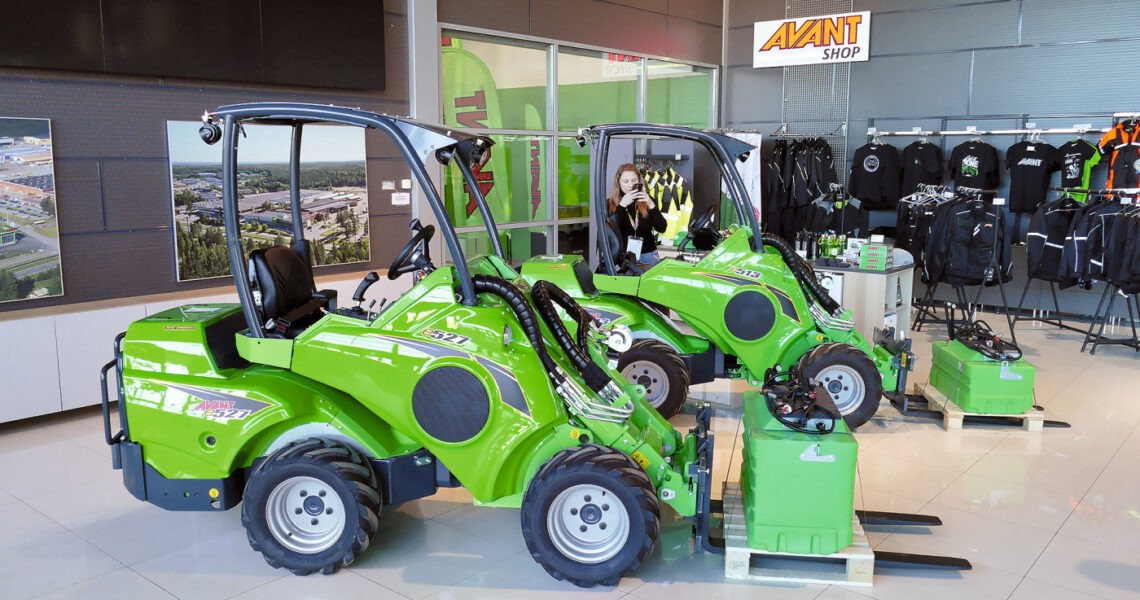
Wie so oft bei kompakten Radladern, liegt deren Ursprung auch bei Avant auf dem Bauernhof, wo es beim Verteilen von Futter-Silage oder beim Ausmisten schon immer großes Potential zur Mechanisierung von ursprünglich schwerer körperlicher Arbeit gab. Im Jahr 1991 konnte Firmengründer Risto Käkelä Teile der Fertigung und des Produktionsprogramms seines damaligen insolventen Arbeitgebers erwerben. Dieser mutige Schritt war zugleich die Geburtsstunde von Avant. Über die Jahre konnte das Familienunternehmen den ursprünglichen Standort durch diverse Zukäufe so erweitern, dass man heute über eine Hallenfläche von 70.000 m² auf einem Areal von 21 ha verfügt. Nun ist Finnland gewiss nicht als Billiglohn-Standort bekannt. Um also die Wettbewerbsfähigkeit zu sichern, gibt es eigentlich nur zwei Wege: Verlagerung von einzelnen Produktionsschritten in Länder mit geringeren Lohnstückkosten oder ein hoher Automatisierungsgrad. Avant hat sich für Letzteres entschieden und erreicht damit eine erstaunliche Fertigungstiefe.
So erzeugt zum Beispiel der Laser-Zuschnitt von Blechen ohne Nachbehandlung sehr saubere und präzise Teile, die sich perfekt für die Weiterbearbeitung in einer Biegemaschine eignen, die wiederum von einem Roboter bestückt wird. Dieses Prinzip zieht sich durch den gesamten Fertigungsprozess: So werden große Teile der Schweißarbeiten, der mechanischen Bearbeitung und der Pulverbeschichtung automatisiert ausgeführt. Was dort nach einer gewissen Zeit auffällt: Es fehlt der typische Geruch einer Maschinenfabrik. Da sämtliche Prozesse in gekapselten Einheiten erfolgen, sind die Beschäftigten keinen Belastungen durch Kühlmittel-Aerosole oder Schweißrauch ausgesetzt.
Besucher wiederum sollten stets darauf bedacht sein, keines der autonomen Flurförderzeuge, die für den Materialfluss sorgen, durch unbedarftes Im-Weg-Stehen zu einer Zwangsbremsung zu zwingen. Wie Vertriebsleiter Mika Järvinen ausdrücklich betont, ging durch die Automatisierung keiner der 380 Arbeitsplätze verloren. Vielmehr konnten Mitarbeiter von schwerer, monotoner Arbeit entlastet werden und helfen jetzt an anderer Stelle dabei, der gestiegenen Nachfrage gerecht zu werden. Etwa bei den Fahrerkabinen, welche die allermeisten Baumaschinen-Hersteller heutzutage von spezialisierten Zulieferern beziehen. Nicht so Avant: Vom Verschweißen der Rahmen bis zur kompletten Bestückung erfolgt alles im eigenen Haus. Auf diese Weise verlassen derzeit gut 165 kompakte Lader pro Woche die Montagelinien.
Wobei: Die Bezeichnung Lader hört Oliver Bonn, Vertriebsmanager bei Avant Deutschland, eigentlich gar nicht so gerne. Tatsächlich wird man damit – angesichts 200 lieferbarer Anbaugeräte und Ausrüstungen – dem Multifunktions-Charakter nicht gerecht. Auf den ersten Blick gleichen die Maschinen zwar dem Konzept der beliebten Hoflader. Bei genauerer Betrachtung fallen jedoch einige gravierende Unterschiede auf. Abgesehen von der Positionierung des Fahrerplatzes auf dem Vorderwagen, besitzt der kleine Finne ein starres Knickgelenk und keine Pendelachse. Achsen sucht man generell vergeblich, hinter jeder Radnabe sitzt ein Radialkolben-Hydraulikmotor von Poclain. Zusammen mit dem sehr tiefen Schwerpunkt sorgt diese steife Konstruktion für eine hohe Standsicherheit, was auf Messen gerne in teils haarsträubenden Manövern demonstriert wird. Dafür, dass im Gelände nicht nur das eine Rad in der Luft frei dreht, sorgt eine clevere Kaskade von hydraulischen Längs- und Quersperren. Auch der außermittige Mono-Teleskoparm ist typisch für einen Avant. Klarer Beweis für den Erfolg dieses Konzepts – neben bislang 90.000 weltweit verkauften Maschinen – ist die Tatsache, dass mittlerweile einige namhafte Wettbewerber Maschinen anbieten, die auffällige Ähnlichkeiten in der Bauform zeigen.
Wegen ihrer kompakten Abmessungen eignen sich diese Maschinen naturgemäß auch für den Einsatz in Innenräumen, wo weder Abgase noch Lärm erwünscht sind. Das gilt besonders in Stallungen, wo in unmittelbarer Nähe von Tieren gearbeitet werden muss.
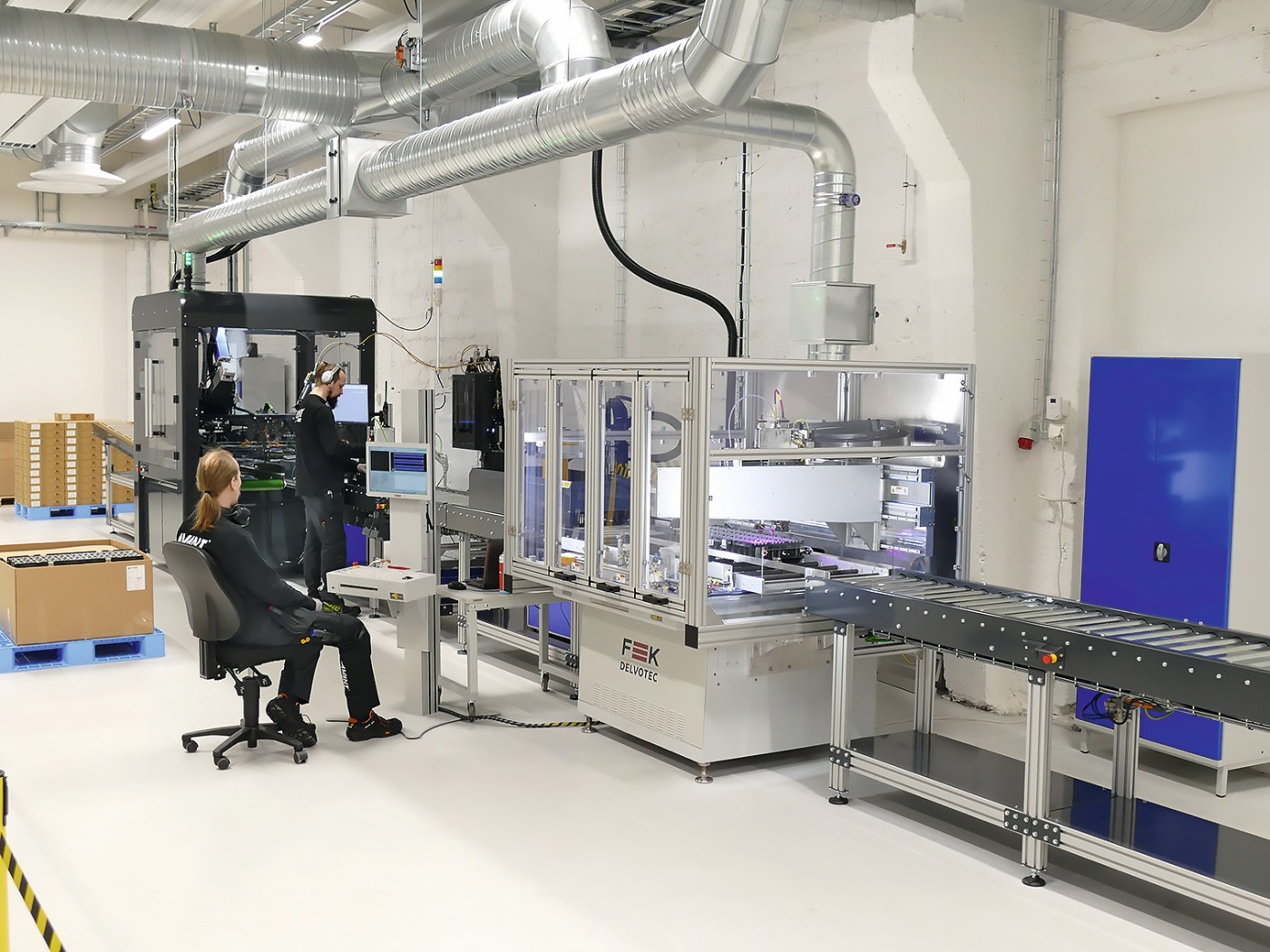
Aus diesen Grunde haben sich die Finnen schon sehr früh mit einem Elektroantrieb beschäftigt. Bereits 1997 wurde eine Akku-Variante des Knickladers angeboten. Mit der seinerzeit verfügbaren Batterietechnik erwies sich die Laufzeit allerdings letztendlich als unbefriedigend und das Projekt E-Lader wurde zunächst wieder eingestellt. Gut zwanzig Jahre später hatten sich die technischen Möglichkeiten weiterentwickelt, gleichzeitig war die Nachfrage nach emissionsfreien Maschinen deutlich gestiegen. Erstmals mit Lithium-Ionen-Batterien ausgestattet, konnten von den zwei Elektro-Modellen rund 700 Stück verkauft werden.
Der Haupt-Kostenfaktor bei allen Akku-Maschinen ist ja bekanntlich die Batterie selbst. Und so hat man sich Gedanken gemacht, wie man hier ein erträgliches Preisniveau erreichen kann. Ergebnis war die Errichtung einer eigenen Batterie-Produktion unter dem Namen Avant-Power in unmittelbarer Nähe zum Stammwerk. Schon die Ankündigung sorgte für vorsichtige Nachfragen von Wettbewerbern, ob man die neuen Akkus als Zukaufteil erwerben könne. Das ist derzeit nicht vorgesehen. Die Fertigungsstraße, die Anfang 2024 in Betrieb gegangen ist, soll zunächst 700 bis 800 Batterien jährlich für den Eigenbedarf produzieren. Jani Käkelä, CEO und Sohn des Firmengründers, sieht im Elektroantrieb gerade bei kompakten Baumaschinen ein großes Potential. So könnte bereits in fünf Jahren jeder zweite verkaufte Avant-Lader ein elektrischer sein – und eigenes Know-how bei der Herstellung von leistungsfähigen Akkus ein gewichtiger Wettbewerbsvorteil.
Was die genaue Konfiguration der Batterien angeht, lässt man sich – verständlicherweise – nur bedingt in die Karten schauen. Grob gesagt werden NMC-Zellen, die geringfügig größer als die haushaltsüblichen AA-Zellen sind, zu Einheiten verbunden, die schließlich mit 44 V Spannung arbeiten. Alle Zellen sind einzeln abgesichert und von einer speziellen Flüssigkeit umgeben. Je nach Lastabnahme und Umgebungstemperatur kann die Batterie hiermit entweder gekühlt oder beheizt werden. Die Einhaltung einer optimalen Betriebstemperatur wirkt sich sowohl günstig auf die Stromabgabe als auch auf die Lebensdauer aus. Sollte es zu einem Defekt einer einzelnen Zelle kommen, wird das Gesamtsystem nur minimal beeinträchtigt. Auch die gefürchtete Ausbreitung eines Brands ist durch die Flüssigkeit so gut wie ausgeschlossen.
Die beiden neuen Elektrolader wiederum werden seit Januar 2024 in Serie produziert. Gegenüber den Vorgängermodellen e5 und e6 sollen die Batterien über eine etwa doppelt so hohe Energiedichte verfügen. Die neuen Typenbezeichnungen weisen auf die jeweilige Batteriekapazität hin, folglich verfügt der e513 über 13 kWh und der e527 entsprechend über 27 kWh. Bis auf die Batterielaufzeit sind die Leistungswerte identisch. Die kleinere Variante (ca. 3 h Laufzeit) wird für Einsätze mit mehrfach über den Tag wiederkehrenden Arbeitszyklen wie etwa in der Landwirtschaft empfohlen. Für einen ganzen Arbeitstag wie in der Bau- und Abbruchbranche ist der e527 (ca. 6 h Laufzeit) die bessere Wahl. Betreiber, die sich solche Laufzeiten schon für ihren e5/e6 gewünscht hätten, haben nun die Möglichkeit für ein Upgrade mit den neuen Batterien. Je nach Ladegerät variieren die Ladezeiten zwischen nur knapp sechs Stunden und nur einer guten Stunde.
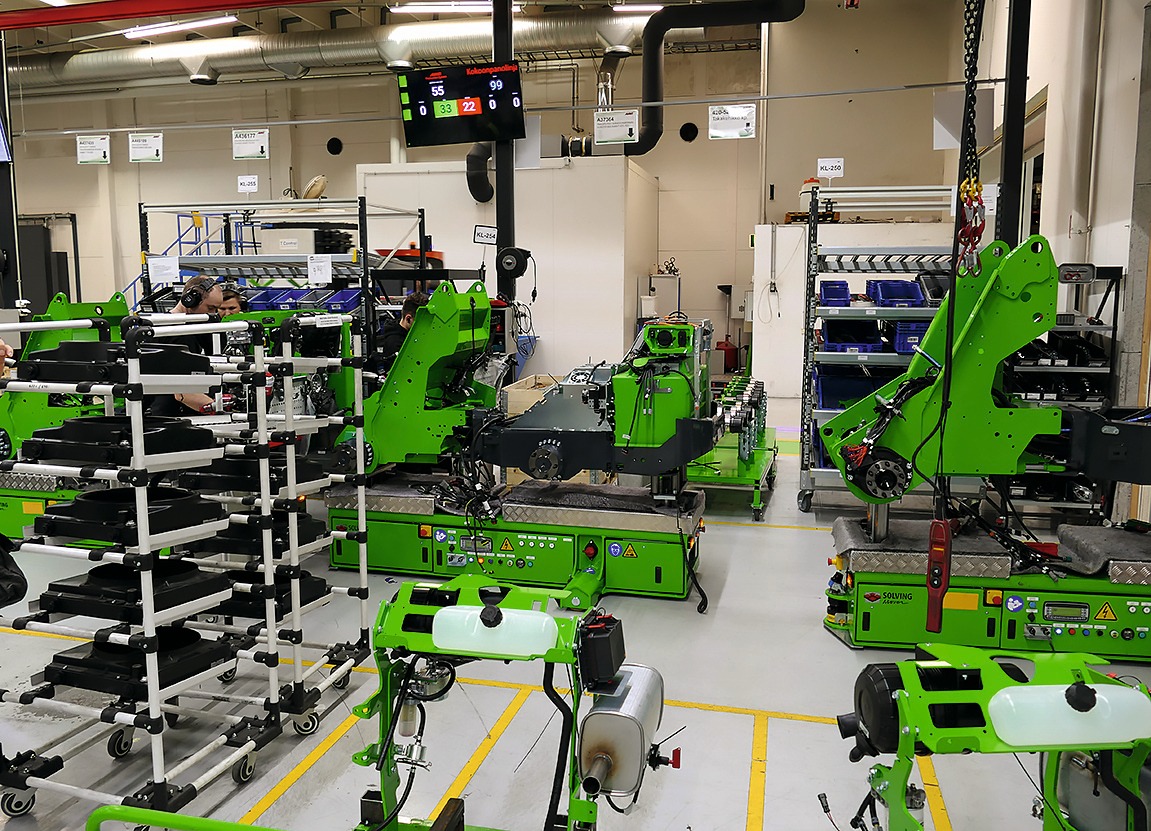
Bei der Entwicklung war man bestrebt, so viele Gleichteile wie möglich aus der Diesel-Variante zu verbauen. So verfügen auch die Elektrolader über einen hydrostatischen Fahrantrieb – den geringfügig geringeren Wirkungsgrad nimmt man zugunsten einer bewährten Technik in Kauf. Und auch beim Anschaffungspreis konnte sich Avant, nicht zuletzt aufgrund der eigenen Batteriefertigung, deutlich an den Preis der Dieselmodelle annähern.
Dem Eindruck beim Probefahren muss vorausgeschickt werden, dass die Testbedingungen mit einem gefrorenen Altschnee-Haufen eher suboptimal waren – dafür wurden die Laderchen eigentlich nicht konzipiert. Die Sitzposition auf dem Vorderwagen ist zunächst etwas ungewohnt, das gab es aber schon bei legendären Radlader-Herstellern. Sollte man unsicher sein, in welcher Stellung sich der Hinterwagen gerade befindet, hilft ein sanfter Umgang mit den Richtungs-Fahrpedalen. Hektisches Drehen am Lenkrad hingegen wirkt, wie allgemein, eher kontraproduktiv. Einmal dann eingegrooved, läuft es rund und man steuert einen agilen und übersichtlichen Lader. Der Elektro-Avant eignet sich bestens für Einsätze, bei denen der Bediener öfter mal absteigen und andere Tätigkeiten ausführen muss, um dann wieder aufzuspringen und mit vollem Tempo weiterzuarbeiten. Das schadet dem Elektromotor, im Gegensatz zum Verbrenner, nämlich überhaupt nicht.
Gleichzeitig wird noch ein anderer Vorteil des Avant-Laders gegenüber dem Skidsteer-Kompaktlader-Konzept deutlich: Während beim antriebsgelenkten Lader die Richtungsänderung immer gegen einen gewissen Zwang in Form von Reibung erfolgt, laufen die Räder des Knicklenkers bei Kurvenfahrt auf festem Boden mit wesentlich weniger Rollwiderstand. Das verlängert insbesondere beim E-Lader die Laufzeit. Wie so oft bleibt der entscheidende Faktor jedoch die Fahrweise. So habe ich es tatsächlich nur einmal geschafft, dass der Lüfter des Kühlsystems angesprungen ist. Dafür bedurfte es aber auch zahlreicher, schnell aufeinander folgender Arbeitsspiele, in denen ich mal herauskitzeln wollte, was in dem Maschinchen steckt. Da der Avant aber eher weniger im Massenumschlag eingesetzt wird, dürfte eine solche Fahrweise nicht sehr repräsentativ sein.
Die Höchstgeschwindigkeit der E-Lader ist auf 10 km/h begrenzt. Bei den frostigen Außentemperaturen lag der Wunsch nach einer geschlossenen Kabine nicht fern. Die soll dann auch ab Ende des Jahres lieferbar sein. Insgesamt war es sehr beeindruckend zu erleben, was das Familienunternehmen aus einem scheinbaren Nischenprodukt in gut drei Jahrzehnten gemacht hat.